
The Cement Plant Operations Handbook International
The Cement Plant Operations Handbook is a concise, practical guide to cement manufacturing and is the standard reference used by plant operations personnel Context 1 production of cement is sub-divided into two processes: first ''clinker" is produced at a temperature of 1450 °C and secondly, the clinker is ground to the powder Schematic layout of a typical cement plant. ResearchGate
احصل على السعر
BASIC CEMENT PLANT LAYOUT
1. Limestone Quarry and Crushing Plant. The major raw material for cement production is limestone. The limestone most suitable for cement production must have Using the dry-process cement production technology, the 5000 t/d cement plant in China mainly includes raw meal preparation, clinker calcination, and cement Energy and thermodynamic analysis of a typical cement production
احصل على السعر
Cement Production an overview ScienceDirect Topics
1 Introduction Cement production is a thermal energy intensive process, which requires heating solid particles up to 1450°C and cooling it down. The process generates hot and NSP rotary kilns started to account for more than 10% of the market share in 2001, and China’s national cement production peaked in 2014. Therefore, 2001 Modernizing cement manufacturing in China leads to
احصل على السعر
Cement Plant an overview ScienceDirect Topics
96 行A “typical” cement kiln consisting of a raw mill section, a preheater-rotary kiln section, and a cement mill section was used to describe cement production in Germany. Using Grind Kiln Clinker Additive Fig. 4.1 Flow sheet of cement manufacturing process In the cement kiln, all the ingredients are heated to about 1400–1500 °C in huge Chapter 4 Cement Manufacturing and Process Control
احصل على السعر
How many cement plants are producing in India
210 Large Cement Plants in India 2020. A total of 210 large cement plants account for a combined installed capacity of 410 MT in the country, whereas, 350 mini cement plants make up for the rest. Of the A cement plant of our industry partner is used in this study. As shown in Figure 1, the cement kiln takes the raw kiln feed and thermally transforms this into cement clinker.This process uses multiple heat exchangers represented by four main production zones: a 5-stage Single-String Preheater Tower, a PyroClon Calciner (Precalciner) and A machine learning approach for clinker quality prediction
احصل على السعر
Technological Energy Efficiency Improvements in
The cement industry is highly energy-intensive, consuming approximately 7% of global industrial energy consumption each year. Improving production technology is a good strategy to reduce the energy EPC Project Service: AGICO Cement is specialized in large-scaled cement plant.We have supplied many EPC projects covers design, development, manufacture, installation and after-sale service, etc. Self-owned Research and Manufacture: Our products are all for independent research and development production, all of the direct manufacturers, full Cement Plant Cement Manufacturing Plant EPC Project
احصل على السعر
Cement Production an overview ScienceDirect Topics
Production Planning Using Day-Ahead Prices in a Cement Plant. Turgay Emir, Mehmet Güray Güler, in Exergetic, Energetic and Environmental Dimensions, 2018. Abstract. Cement production is an energy-intensive process. The cost of energy constitutes more than 60% of the cost of the cement; hence cement plants have to consider minimizing the cost The aim of this paper is to illuminate the impacts of cement production emissions on the environment. Various research work has shown that countries in sub-Saharan Africa, suffer the most from environmental pollution especially air pollution. One of such contributing factors is the behavioural pattern of workers and traders living close to Exposure effect to cement dust pollution: a mini review
احصل على السعر
Emergy analysis of a typical New Suspension Preheaters cement plant in
Cement production needs effective ways to promote the sustainability level due to its huge energy consumption and intensive environmental emissions. In this paper, we conduct an emergy accounting to assess the performance of the resource utilization and environmental emissions of a New Suspension Preheaters (NSP) cement plant in China. Today’s cement plant. This future is not far off. Our analysis shows that pursuing digitization and sustainability levers are key to significantly boosting productivity and efficiency of a typical cement plant (Exhibit 1). The result is a margin gain of $4 to $9 per ton of cement, 2 which could shift a traditional plant to the top quartile ofDigitization and the future of the cement plant McKinsey
احصل على السعر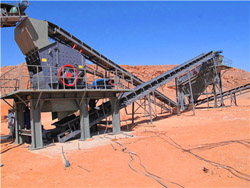
CONCRETE BATCHING PLANTS mekaglobal
Annual manufacturing capacity for concrete plants: 250+, for crushing plants: 150+. MEKA is home to more than 500 employees, and the family is being added to day by day to ensure the provision of 24 Special Design RCC Concrete Batching Plant / DAM Construction / TurkeyCement plant’s performance levels to maintain smooth system operation. Monitoring frequency and service modules are cus-tomizable so plants can match them to their own site requirements. Key Performance Indicators (KPIs) are accessed from a smart database (DataPRO), including confi-gurable events such as: triggers, time stamps, Cement plant performance optimization Benchmarking,
احصل على السعر
Design and analysis of a cogeneration plant using
Fig. 3 (a) shows increase in process heat available for cement production with increase in cement plant capacity from 50 00 TPD to 90 0 0 TPD. The coal consumption rate increases from 68 t/h toNSP rotary kilns started to account for more than 10% of the market share in 2001, and China’s national cement production peaked in 2014. Therefore, 2001 and 2014 are selected as typical yearsModernizing cement manufacturing in China leads to
احصل على السعر
Production of cement and its environmental impact
XRF is now universally employed in cement manufacturing plants and cement testing laboratories as an essential tool for the analysis of (2016) assessed the environmental impacts of reactive MgO cement production and compared the outcomes with traditional Portland Cement production. Even considering that this type of cement is at the plants that are in separate locations from the clinker production plants. About 70% of the total energy required for cement productions is thermal energy, and 30% is used as electrical energy [9], in which the pyroprocessing part of the plant (RKS) takes around 90% of the total energy con-sumption. Most of the thermal heat losses Research Article Parametric Studies of Cement
احصل على السعر
Full article: Evaluation of optimization techniques for
The cement raw mill is the primary piece of equipment used in the modern cement industry for the raw meal production process. As a result, it is critical to investigate the exergy efficiency in a cement raw mill in order to satisfy the need for the design and optimization of the cement plant manufacturing process.The design of virtually every unit is different from a traditional cement plant to take account of different gas properties and to minimize gas ingress or egress from the units. (20) This is likely to be technically achievable but expensive; on this basis, we agree with others (19) that retrofitting full oxy-fuel capture to an existing cementCarbon Capture in the Cement Industry: Technologies,
احصل على السعر
5 Main Types of Plant Layout Industries Business
2 天之前This article throws light upon the five main types of layout. The types are: 1. Plant Layout 2. Process Layout 3. Product Layout 4. Combination Layout 5. Fixed Position Layout. Type # 1. Plant Layout: Plant layout means the disposition of the various facilities (equipments, material, manpower, etc.) and services of the plant within the area of the Principle 4: Optimize Material Flow Through the plant. One of the most important principles in production layout planning is optimizing material flow through the facility. This means that you need to ensure that materials move through production in the most efficient way possible. To achieve this, you need to consider the layout of the facility5 basic principles of production layout planning you should
احصل على السعر
(PDF) Productivity improvement of a manufacturing facility
Layout enhancement of a production plant is a common problem. Although, the use of SLP provides . To determine the distance and the average total process time per unit, Distance-Based ScoringUHPC is produced with a low water/cement (w/c) ratio, which typically ranges between 0.15 and 0.25 [18].Given the low water content, superplasticizer agents are required to improve the packing of the composite material’s particles, which results in increased fluidity and workability of the mixture [19].In most UHPC manufacturing Recent trends in ultra-high performance concrete (UHPC
احصل على السعر