
Ball milling: a green technology for the
Ball milling is a mechanical technique widely used to grind powders into fine particles and blend materials. 18 Being an environmentally-friendly, cost A ball mill is a type of grinder widely utilized in the process of mechanochemical catalytic degradation. It consists of one or (PDF) Grinding in Ball Mills: Modeling and Process
احصل على السعر
Ball-milling: A sustainable and green approach for starch
Various mills are used to grind grains and refine processes, including stone, disc, roller, hammer, and ultra-fine [1]. Stone and hammer mills are usually single To illustrate how grinding conditions can affect ball mill efficiency, the batch grinding model will be used to model closed-circuit ball milling of the soda-lime glass. For The energy efficiency of ball milling in comminution
احصل على السعر
Choosing the right strategy: cryogrinding vs. ball milling comparing
Comparing the crystallinity of chitin after cryogrinding with that after BM, we noticed a high dependency on size and mass of the grinding balls. 11,15 Thus, Margoutidis et al. Ball milling is a simple, fast, cost-effective green technology with enormous potential. One of the most interesting applications of this technology in the eld of cellulose is the Ball milling: a green technology for the preparation and
احصل على السعر
Used Ball Grinding Machine China Trade,Buy China Direct From Used Ball
Ball Mill Grinding Machine Used For Silicate,Limestone,Cement Clinker,Copper,Iron Ore,Stone,Rock. Henan Xingyang Mining Machinery Manufactory. US $4300-$4500 / set A ball mill is a type of grinder used to grind and blend bulk material into QDs/nanosize using different sized balls. The working principle is simple; impact and attrition size reduction take place as the ball drops from near the top of a rotating hollow cylindrical shell. The nanostructure size can be varied by varying the number and size ofBall Mill an overview ScienceDirect Topics
احصل على السعر
Ball-milling: A sustainable and green approach for starch
Ball-milling is a low-cost and green technology that offers mechanical actions (shear, friction, collision, and impact) to modify and reduce starch to nanoscale size. It is one of the physical modification techniques used to reduce the relative crystallinity and improve the digestibility of starch to their better utility.Ball milling is a mechanical technique that is broadly used to grind powders into fine particles [134–141]. The reactants are generally broken apart using solvent molecules in the traditional method; but in ball milling, reactants are broken by using mechanical forces. The term mechanochemistry has been introduced very recently [142].Ball Milling an overview ScienceDirect Topics
احصل على السعر
Ball milling A green and sustainable technique for the preparation
Ball milling is a mechanical technique used to grind powders into fine particles [1]. Generally, a ball mill consists of a hollow cylindrical vessel that rotates around its axis and balls which are made of materials such Furthermore, ball milling may be used to manufacture metal powders from waste metals. The process of ball milling involves the grinding and mixing of metal particles within a ball mill, which is a type of equipment used for grinding, with the aim of producing a fine powder . This method has been widely employed in the manufacturing of metalProducing Metal Powder from Machining Chips Using Ball Milling
احصل على السعر
Modeling and Simulation of Ultrafine Grinding of Alumina in
Mineral liberation from ores is an important step in mineral processing. It is necessary to grind the ore to extremely fine size to liberate the mineral from such ores. The planetary ball mill is promising in that it makes grinding to submicron sizes possible by imparting high energy to the ground powder. In this context, there is a need to The current production method of nanobiochar (NBC), an emerging, environmentally friendly nanocarbon material, is tedious and lengthy. Therefore, in this study we aimed to improve the productivity of NBC via high-energy ball milling by manipulating the grinding media and processing time. The particle size distribution of the resulting NBC Nanomaterials Free Full-Text High-Energy Ball Milling for
احصل على السعر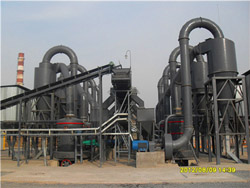
Synthesis of Metal Organic Frameworks by Ball-Milling
The initial ball milling method is a neat grinding method, which is a method in which the product is directly obtained by directly mixing ball milling with solid raw materials. In 2006, Pichon et al. first synthesized porous MOF copper isotonic acid Cu(INA) 2 by mechanical ball milling. Since then, this method has attracted much attention.In this paper, the wet ball milling process was used in the laboratory ball milling test. Before grinding, the ball mill was kept idle for 10 minutes and then washed together with the grinding media. Three types of ores were crushed and separated by a jaw crusher, and the ground particle size of -2 mm was selected.The Effect of Grinding Media on Mineral Breakage Properties
احصل على السعر
Particle morphology control of metal powder with
Section snippets Experimental. Mechanical milling was performed by using a planetary ball mill (PBM) under various experimental conditions. Copper powder (99.0% purity, median particle size x 50 = 45 μm, Aldrich chemistry) was used as shown in Fig. 1. Mechanical alloying (MA) was carried out at two types of rotation speeds: low (10, 50, Largest balls should be just heavy enough to grind and break down the largest and hardest particles. [1, p.57] [4] Shape of milling media can be rods or barrels in addition to the balls. Balls have greater surface area which makes them better for particle size reduction. Ball milling type is dependent on the type of ball mill used. HighBall milling as a synthesis method Aalto University Wiki
احصل على السعر
Ball Mill an overview ScienceDirect Topics
The ball mill process is a mechanical-chemical process that uses mechanical force to induce the chemical and structural change of certain materials (Amusat, Kebede, Dube, & Nindi, 2021). A mechanical mill is a type of grinder used to grind and blend a bulk material into extremely fine nanosize powder using different sizes of milling balls.1. Introduction. The term chemical additives or grinding aids (GAs) refers to any substance which results in increased grinding efficiency and reduction in power consumption when added to the mill charge (amounts not exceeding 0.25 wt.% of the feed) during grinding [1], [2], [3].The use of grinding aids to increase mill throughput is quite A critical review on the mechanisms of chemical additives used
احصل على السعر
Process engineering with planetary ball mills RSC Publishing
Planetary ball mills are well known and used for particle size reduction on laboratory and pilot scales for decades while during the last few years the application of planetary ball mills has extended to mechanochemical approaches. Processes inside planetary ball mills are complex and strongly depend on the processed material and synthesis and, thus, the A pharmaceutical ball mill is a type of grinder used to grind and blend materials while manufacturing various dosage forms. The size reduction is done by impact as the balls drop from near the top of the shell. Ball mills are used primarily for single-stage fine grinding, regrinding, and as the second stage in two-stage grinding circuits.Ball Mill Principle, Construction, Working, and More Soln
احصل على السعر
Mechanochemical activation of natural clay minerals: an
Smaller milling balls provide higher frictional forces and thus are useful for amorphisation or the formation of metastable phases, (Suryanarayana 2001). Typically, grinding balls are made of stainless steel, special metals, corundum, zirconia, carbides, etc., (Suryanarayana et al. 2001). A short list of various used ball sizes is shown in Table 2.High performance milling media is one of the most commonly used ceramic materials for milling. These balls are hard corrosion resistant. The alumina grinding / milling media balls are extensively used in the fields of Paints, Inks, Geology, Metallurgy, Electronics, Ceramics, Glass, Refractory, and Chemical Engineering. Density: 3.6 g/cm 3Milling Media: Factors for choosing milling media for planetary
احصل على السعر
(PDF) On the Use of Ball Milling for the Production of
The average density of the mixture of ball-milled collagen and alumina particles was reduced by about 1.20% after ball milling for about 100 h. The stir casting technique was employed to developMSE Supplies provides quality, durable, and high-performance milling media. Milling balls made of steel and ceramic are our most popular materials. If you have questions regarding MSE Supplies milling media, please request a quote, contact us online, or call us at (520)789-6673 today. Our in-house experts are ready to help you select the bestMilling Balls Grinding Media & Grinding Balls MSE Supplies
احصل على السعر
(PDF) Grinding Media in Ball Mills-A Review ResearchGate
One of the most used tumbling mills is the ball mill. This paper reviews different types of grinding media that have been developed and improved over the years and their properties. Also reviewed
احصل على السعر