
Mine operating costs and the potential impacts of energy and grinding
The study looks at patterns in mining type, mill processing type, mineral type, and the differences between costs expressed in feasibility studies vs. operating mineral processing, art of treating crude ores and mineral products in order to separate the valuable minerals from the waste rock, or gangue. It is the first process that most ores undergo after mining in order to provide a Mineral processing Metallurgy, Crushing
احصل على السعر
(PDF) OVERVIEW OF GRINDING SYSTEMS AND MV DRIVE
Grinding of ore is one of the most important and power intensive operation in mining. In order to process the ore at faster rate, sizes of mills have gone bigger and The grinding process in ball mills is notoriously known to be highly inefficient: only 1 to 2% of the inputted electrical energy serves for creating new surfaces. Reducing the energy footprint of grinding circuits: the
احصل على السعر
Energy Use of Fine Grinding in Mineral Processing SpringerLink
Fine grinding, to P80 sizes as low as 7 μm, is becoming increasingly important as mines treat ores with smaller liberation sizes. This grinding is typically done The operation and mechanism of grinding and size reduction is explained with the help of solved mathematical examples. Computation for determining SAG power index is Mineral Processing Design and Operations ScienceDirect
احصل على السعر
Safe, Reliable and Efficient Crushing and Grinding in Mining Operations
In mining operations, the comminution process reduces the mined solid materials through crushing, grinding and other means. SAG and Ball mills are one of the The Complex Orebodies Program (COB) supported the early development of this industry–research partnership. Crushing and grinding rock (comminution) in the processing stage is incredibly energy Increasing energy efficiencies in mineral
احصل على السعر
Mine operating costs and the potential impacts of energy and grinding
Most notably, the cost apportioned to the mine operations was notably higher for underground (51.1 ± 11.4%) than for open pit (40.3 ± 4.6%), with mines employing both techniques in between (47.9 ± 5.9%). The median values shown in Table 4 suggest the influence of outliers at the lower end, particularly for the underground mining operations.The grinding process in ball mills is notoriously known to be highly inefficient: only 1 to 2% of the inputted electrical energy serves for creating new surfaces. There is therefore obvious room for improvement, even considering that the dominant impact mechanism in tumbling mills is a fundamental liability limiting the efficiency.Reducing the energy footprint of grinding circuits: the
احصل على السعر
Reduction of Fragment Size from Mining to Mineral
2.1 Energy. Rock drilling, blasting, and comminution (crushing and grinding) consume a vast amount of energy in hard rock mines. As mentioned in Sect. 1, statistics from hard rock mines indicates that drilling and blasting consumes 2% and comminution does 53% of the total energy input in the whole production chain from The Mining Process. Gold at Macraes is known as ‘refractory ore’, which means it is ultra-fine and resistant to the typical cyanide leach process. The mining process at Macraes is circular and follows a cycle of exploration, mining, processing and rehabilitation and closure. With a 30-year history of development spanning fluctuating goldThe Mining Process OceanaGold
احصل على السعر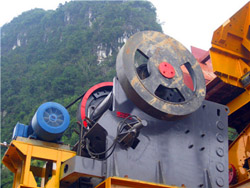
Grinding Mill Circuits A Survey of Control and Economic Concerns
Nearly half of the world's milling circuits use ball mills, while almost 90 % of the mining operations use balls as grinding devices [4]. Grinding balls are produced from materials with highContribute to crush2022/mill development by creating an account on .mill/sbm basic grinding machine operation.md at main
احصل على السعر
Modeling of Bauxite Ore Wet Milling for the Improvement of
Size reduction is a necessary operation in mineral processing plants and provides the desired size for separation operations and the liberation of the valuable minerals present in ores. Estimations on energy consumption indicate that milling consumes more than 50 % of the total energy used in mining operations. Despite the fact that ball Semi-autogenous grinding mills play a critical role in the processing stage of many mining operations. They are also one of the most intensive energy consumers of the entire process. Current forecasting techniques of energy consumption base their inferences on feeding ore mineralogical features, SAG dimensions, and operational variables. Machine Learning and Deep Learning Methods in Mining Operations
احصل على السعر
Machine Learning and Deep Learning Methods in Mining Operations
The paper from Avalos et al. (2020), presents the adoption of ML in mining operations to optimize energy demand in a mill at a mine in Chile. The work proposes a methodology using real-timeAn estimated consumption of steel grinding media of around 600,000 tons p.a. in the 1980s already gives an indication of the scale of the problem (Malghan, 1982). Likewise, in the cement industry, as mills are supplied for ever increasing capacities, the ball size distribution and wear exact a tremendous effect on the profitability of producingConsumption of steel grinding media in mills A review
احصل على السعر
Gold extraction QueensMineDesignWiki
The costs associated with power supply, grinding media, and liners used in comminution circuits almost always represent the single largest cost in gold extraction processes (Mosher, 2005). Thus, the This work considers a chain from mine to non-aqueous mineral processing operations, with a special focus on management of fine-grained (<50 µm) material (Fig. 1).The objective is to provide an overview and some selected examples of potential methods for energy-efficient production of valuable materials from complex ores, consider ways of Towards waterless operations from mine to mill ScienceDirect
احصل على السعر
11.24 Metallic Minerals Processing U.S. Environmental
The emission factors in Tables 11.24-1 and 11.24-2 are for the process operations as a whole. At most metallic mineral processing plants, each process operation requires several types of equipment. A single crushing operation likely includes a hopper or ore dump, screen(s), crusher, surge bin, apron feeder, and conveyor belt transfer points.Abstract and Figures. The first process that most of the ores or minerals undergo after they leave any mine, is mineral processing or mineral/ ore dressing. It is a process of ore preparation(PDF) Overview of Mineral Processing Methods ResearchGate
احصل على السعر
Mining and materials production Energy Technology IEA
Demand for each of the five key critical minerals increases 1.5 to 7 times by 2030 in the Net Zero Emissions by 2050 (NZE) Scenario as clean technology deployment soars. Greater material efficiency across all demand segments can more than offset increased steel and cement demand for clean energy technologies and infrastructure.In mining operations, crushing and grinding of coarse rock into smaller particles CE 3.0), the mineral processing field struggles to advance from the basic CE requirements (i.e, CE 1.0 to CE 2Mine operating costs and the potential impacts of energy and grinding
احصل على السعر
ABB process control and automation solutions for mines
Automation is not new to mining, but it is generally more basic in mines than in other industries and is often limited to simple control of motors, equipment or certain parts of processes. Further, mines tend to have a large number of independent pieces of equipment and systems from different suppliers.This chapter is an introductory chapter to the world of mining, its origin, its relevance to modern industry, and personal use, along with its major contributions to various national economies. The chapter also includes a section on the phases and processes in large-scale open-pit mining operations. Keywords. Open-pit mining; History of miningIntroduction: Managing Large-Scale Mining Operations
احصل على السعر
(PDF) Comminution in mineral processing ResearchGate
the common operation for grinding is attrition[14] (Figure 4.1). Figure 4. 1 Concept behind crushing and grinding (Image- TON) Comminution in mineral processingMining operations are also often conducted in remote locations where access to spare parts and large maintenance facilities may be difficult. Current research has focused on the development of sensor systems that can be incorporated into large vehicles and heavy machinery to monitor continuously the “state of the health” of the vehicle.3 Technologies in Exploration, Mining, and Processing
احصل على السعر