
Vertical mill simulation applied to iron ores ScienceDirect
This type of mill is now attracting interest in primary grinding applications, due to its higher efficiency when compared to ball mills, which are usually used at this stage. In this study, a coarse sample of iron ore was tested in a pilot scale grinding circuit with a The application of vertical-roller-mills (VRM’s) for ore grinding is part of the second strategy. The grinding parts of a Loesche mill (Fig. 1) are a rotating table (1) with Research of iron ore grinding in a vertical-roller-mill
احصل على السعر
Research of iron ore grinding in a vertical-roller-mill
For the grinding tests, a Loesche mill LM4.5 (table diameter 0.45 m) is used (Fig. 2 a). This pilot scale mill is a special development for ore grinding, which is Fitting the population balance model of batch grinding to data from a 25.4 cm mill in size reduction of an iron ore from Brazil Optimization of Solids Concentration in Iron Ore
احصل على السعر
Investigation on Iron Ore Grinding based on Particle Size Distribution
The iron ore blend takes RT of 13 min when grounded in the BBM for 250% circulating load with 80% passing particle size of 56 µm. The blend iron ore sample Parameters describing the variation of the median fracture energy with particle size of the UFRJ mechanistic ball mill model have been back-calculated on the Mechanistic modeling and simulation of grinding iron ore
احصل على السعر
Comminution and classification technologies of iron ore
Abstract Hematite and magnetite, the two predominant iron ores, require different processing routes. High-grade hematite direct shipping ores generally only An iron ore concentrate sample was ground separately in a pilot-scale HPGR mill in multiple passes and a dry open-circuit ball mill to increase the specific surface area of particles. Grinding iron ore concentrate by using HPGR and ball mills
احصل على السعر
Development of a Novel Grinding Process to Iron Ore
1 Introduction Modern iron ore pelletizing process operations may be divided into two main process sections: feedstock preparation and agglomeration sensor to measure the related data, i.e., applied load, torque generated, roll speed, specific energy consumption and roll gap in real-time basis with an on-line Potential of High-Pressure Grinding Roll (HPGR) for Size
احصل على السعر
Mechanism of magnetite iron ore concentrate morphology
The grinding method and its associated parameters strongly affect the physical properties of the iron ore concentrate. Ball milling (BM) and High-pressure grinding rolls (HPGR) are commonly employed for grinding iron ore concentrate [18], [19], [20]. In BM, the particle size was decreased by impact and attrition breakage, whereas size In Fig. 1 C, grinding iron ore only produced the finest fraction, followed by the 25 % quartz and 75 % iron ore ratio, equal quantity of the two ore samples, and only quartz material. The 75 % quartz and 25 % iron ratio yielded coarser fractions than quartz only in the range of 150–300 µm. It is evidently observed that the addition of quartz Predicting mill feed grind characteristics through acoustic
احصل على السعر
Comminution and classification technologies of iron ore
Iron ore grinding and classification8.3.1. While there are not HIG mills operating in iron ore applications, globally this technology is used in copper and gold circuits to reduce a F80 under 150 µm to a P80 of ∼30 µm, and in some cases even finer (down to 10 µm in a regrinding circuit duty). Cement Data Book-International Process2.1 Experimental Design. The experimental planning with selected key factor like operating gap (X 1), applied load (X 2) and roll speed (X 3) was designed by CCD method to obtain the optimum conditions for grinding the BHQ iron ore in HPGR.A full second-order polynomial model was obtained by regression analysis for three factors by Potential of High-Pressure Grinding Roll (HPGR) for Size
احصل على السعر
Developments in iron ore comminution and classification
The Zourerat iron ore mine has two 1.7 m diameter × 1.8 m wide HPGR units treating 1400 t/h each of aerofall mill pebbles. The feed is − 25 + 1.6 mm and has a ball mill work index of 12–14 kWh/t. The iron ore has low to moderate abrasion characteristics. Figure 8.21 shows the Zourerat iron ore flowsheet.The modification of magnetic properties of siderite ore by microwave energy resulted in increasing the efficiency of their magnetic separation. Pre-treatment in a microwave oven with maximum power of 900 W of weakly paramagnetic ore (25.1% Fe, 9.6% SiO 2) was realized with the samples (100 g) of iron spathic ore of particle size Iron ore grindability improvement by microwave pre-treatment
احصل على السعر
Vertical mill simulation applied to iron ores ScienceDirect
Abstract. The application of vertical mills in regrind circuits is consolidated. This type of mill is now attracting interest in primary grinding applications, due to its higher efficiency when compared to ball mills, which are usually used at this stage. In this study, a coarse sample of iron ore was tested in a pilot scale grinding circuitKeywords: iron ore; ball mill; modeling; simulation; population balance model; slurry density 1. Introduction It has been well over half a century since Austin and Gardner [1], followed by Reid [2], applied the concept of first-order breakage kinetics to steady-state continuous grinding in a mill. The grindingOptimization of Solids Concentration in Iron Ore Ball
احصل على السعر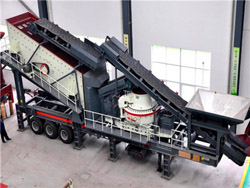
Feed hardness and acoustic emissions of autogenous/semi
In this study, the relationship between acoustic emissions and hardness of different rock types (model quartz, model calcite, and real iron ore) coupled with binary mix ratios of model quartz and iron ore (1:3, 1:1 and 3:1) was investigated in a laboratory-based AG/SAG mill. The acoustic emission response and sensitivity of the mill wereFor fine-grained iron oxide minerals, the iron oxide minerals distribution of 80–100% composition class differed by 22% at −75 + 53 μm size fraction with the two grinding methods, and its(PDF) Process Mineralogical Assessment of the Grinding
احصل على السعر
Optimization of Solids Concentration in Iron Ore
Important advances have been made in the last 60 years or so in the modeling of ball mills using mathematical formulas and models. One approach that has gained popularity is the population balance A typical high-alumina containing iron ore slime from the eastern Indian sector containing 58.13% Fe, 6.48% SiO2, 4.9 % Al2O3 and 5.35% LOI, have been evaluated to find out whether grinding of the(PDF) Characterization and Comminution Studies
احصل على السعر
Exploring ball size distribution in coal grinding mills
The ball size distribution (BSD) in a mill is usually not known, as the measurement of the charge size distribution requires dumping the load and laboriously grading the balls into size classes. Fortunately we had one set of data as discussed below. The general non-availability of BSD necessitates the use of ball wear theory to estimate For example, digital technologies and data storage require considerable increases in the consumption 2013, Iravani et al., 2020 showed that for iron ore, magnesite and limestone, around 50 % weight of the Waste rocks occupy space from ore in the grinding mill, thus lowering the mill’s ore grinding capacity and mineral Towards waterless operations from mine to mill ScienceDirect
احصل على السعر
Reduction of Fragment Size from Mining to Mineral
2.1 Energy. Rock drilling, blasting, and comminution (crushing and grinding) consume a vast amount of energy in hard rock mines. As mentioned in Sect. 1, statistics from hard rock mines indicates that drilling and blasting consumes 2% and comminution does 53% of the total energy input in the whole production chain from This industrial scale study compares two grinding circuits operating in an iron ore process with a production capacity of 12 million tons per year. The plant has three identical parallel lines, all fed from the same feed pile. Each line has an independent grinding circuit, with two ball mills and three hydrocyclones batteries.Evaluation of grinding circuits for iron ore SciELO Brasil
احصل على السعر
(PDF) Eco-Efficient and Cost-Effective Process Design for
Reducing Grinding Energy and Cost -Magnetite Iron Ore Design Case Study. Efficiency of the comminution operations is traditionally assessed based on operating cost and energy consumption• Train critical mill staff experience SGS Minerals Services has run over 20 semiautogenous grinding (SAG) and metallurgical pilot plants on iron ores, including extremely large plants treating up to 1,000 tonnes of ore and lasting for 6 months. Many complex circuits using autogenous grinding, de-sliming, magnetic separation, gravity Metallurgical Testing for Iron Ore SGS
احصل على السعر
Modeling comminution of iron ore concentrates in
High-pressure grinding rolls reached great popularity for pressing iron ore concentrates since its first application in the 1990s. For this particular application, mathematical models describing HPGR performance on the basis of operating conditions and feed characteristics have successfully been used by the authors to map industrial and plant scale mills (0.416 and 5.18 m diameter, respectively) from data obtained in the 25.4 cm diameter mill. Finally, with this scale-up procedure it was possible to appraise the plant scalePopulation balance model approach to ball mill
احصل على السعر