
The Cement Manufacturing Process Thermo
Cement manufacturing is a complex process that begins with mining and then grinding raw materials that include limestone and A cement mill (or finish mill in North American usage) is the equipment used to grind the hard, nodular clinker from the cement kiln into the fine grey powder that Engineering:Cement mill HandWiki
احصل على السعر
Cement Production: How Cement Is Manufactured CEMEX UK
Raw material mill. This takes places in vertical steel mill, which grinds the material through the pressure exerted by three conical rollers. Which roll over a turning milling table. Many factories nowadays prefer to use ball mills for cement grinding, since this kind of mill has small product particle size distribution and is easy to operate. The working principle How Is Cement Produced in Cement Plants Cement Making
احصل على السعر
How Cement Is Made
The first step is to quarry the principal raw materials, mainly limestone, clay, and other materials. After quarrying the rock is crushed. This involves several stages. The first crushing reduces the rock to a maximum size of Cement Milling. Cement milling is usually carried out using ball mills with two or more separate chambers containing different sizes of grinding media (steel balls). Grinding Cement Milling Understanding Cement
احصل على السعر
Cement Finish Milling (Part 1: Introduction & History)
Introduction Cement is manufactured by heating a mixture of ground limestone and other minerals containing silica, alumina, and iron up to around 1450 C in cement mill operations in four ways: • More consistent quality (grade). The continual monitoring of the mill loading and the adjustment of the feed and separator Industrial : Optimization for the Cement Industry ABB
احصل على السعر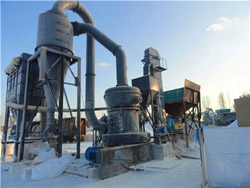
Cement grinding optimisation ScienceDirect
Due to limitation of the mill’s rotational speed, the smallest ball size is usually restricted to about 15 mm. Cement grinding using stirred mills (Pilevneli and Azizli, 1999) indicates that using smaller media (5–8 mm range) improves grinding energy efficiency up to 50% using stirred mills. For specialized types of cement, which are finerthe mill and the balance of material flows through the system, it is possible to identify situations when the feed to the mill and the output can be increased. Increased output over extended periods of time has been observed on mills controlled by Expert Optimizer. • Reduced power consumption. This important saving is a result of the softerIndustrial : Optimization for the Cement Industry ABB
احصل على السعر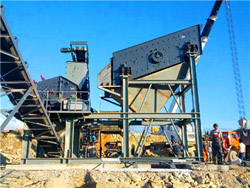
How Is Cement Produced in Cement Plants Cement Making
Generally, the proportion of components in cement raw materials is 67-75% limestone, 10-15% clay, 0.5-1.5% iron ore and 8.5-11% coal. The laboratory of a cement plant. With the help of vertical roller mills or other types of crushers, the raw materials are blended and further ground into smaller pieces of raw meal in the cement plant.You've already forked mill 0 Code Issues Pull Requests Packages Projects Releases Wiki Activity master. mill / sbm how do gold mills work.md. 21 KiB Rawmill/sbm how do gold mills work.md at master mill
احصل على السعر
(PDF) Cement Manufacturing Process and Its Environmental
The cement industry is one of the major contributors to global greenhouse gas emissions, accounting for approximately 8% of total anthropogenic CO 2 emissions. Apart from CO 2 emissions, cementThe working principle of vertical roller mills is relatively simple. In a rotating drum, grinding media (steel balls or ceramic beads) are fed through the mill’s inlet, and the particles are ground into smaller sizes by the mechanical forces generated by the motion of the drum. The ground material is then passed through a classifier, whichHow does vertical roller mill work? ball mills supplier
احصل على السعر
What Are the Parts of a Cement Mills?
A cement mill is a fundamental component of the cement manufacturing process, playing a vital role in breaking down and grinding cement clinker into fine powder. This finely ground powder, when mixed with other materials, produces the building material we commonly know as cement. To achieve this crucial transformation, a cement mill Cement manufacturing is a complex process that begins with mining and then grinding raw materials that include limestone and clay, to a fine powder, called raw meal, which is then heated to a sintering temperature as high as 1450 °C in a cement kiln. In this process, the chemical bonds of the raw materials are broken down and then they areThe Cement Manufacturing Process Thermo Fisher Scientific
احصل على السعر
Cement Mill Cement Grinding Machine AGICO
Coal mill is the main equipment in the pulverized coal preparation process.Because calcining top-grade cement clinker requires a stable supply of coal powder as the fuel of cement kiln, and more than 85% of Posts Related to coal mill how it works » concrete crusher how do they work » joshua hendy iron works rock crusher tiger how does crushing milling works-Stone Crusher How Does A Jaw Crusher Works Crusher Mills, Cone how does a sag mill work Crushing project. how does a sag mill work.Micronizer How Does A Sag Mill Work Crusher Mills
احصل على السعر
how does a grinding cement mill work LinkedIn
Overall, the grinding process in a cement mill is a continuous process that involves the grinding of the raw materials and the separation of the fine particles from the larger ones. The efficiencyCement production process typically involves: •. grinding limestone (and other raw materials to achieve the right chemical composition) to about 90% passing 90 μm in a dry circuit, •. making cement by the chemical reaction between the components of the ground mixture. This chemical reaction occurs at high temperature in a rotary kiln, •.Cement grinding optimisation ScienceDirect
احصل على السعر
sbm/sbm cement mill how stuff works.md at master sbm
You've already forked sbm 0 Code Issues Pull Requests Packages Projects Releases Wiki ActivityOnce the water and the powder mix, they react together and produce compounds known as calcium silicate hydrate (CSH), also known as cement hydrates. “Cement hydrates are small, on the nanoscale scale,” says Tingtao Zhou, a PhD student in the Department of Physics and the lead author of the paper. “These are the building Exploring the effects of moisture and drying on cement
احصل على السعر
The Manufacturing Process of Cement in Factory Mir Cement
Depending on the manufacturer’s process, the grinding is done wet, dry, or semi-dry. In vertical shaft ball mills, 65% of the particles are smaller than 45 microns, and the balls used are around 12mm in size. The rotational speed can vary between 60 80 RPM. A typical ball mill can generate 3500 tons of cement per hour.Portland cement is the most common type of cement and one of the most important ingredients in concrete. Concrete, on the other hand, is the most used building material worldwide just behind the water with an increasing usage trend in infrastructure for the upcoming years. During the production process of cement, massive CO2 emissions A Contribution towards a More Sustainable Cement: Synergy of Mill
احصل على السعر
Concrete Milling 101 What is the concrete milling process?
Concrete milling is the process of removing the top layers of a concrete surface. It’s carried out using scarifying machines equipped with diamond-tipped blades. Milling operations are effective at creating level, smooth surfaces that provide a lot of traction. Plus, the material that’s chipped away can be repurposed for aggregate material
احصل على السعر