
Global Cement Top 100 Report 2017 2018
In 2017 China Resources operated 42 clinker production lines and 91 grinding plants across seven Chinese Provinces, predominantly in the far south and China Clinker Grinding Plant manufacturers Select 2023 high quality Clinker Grinding Plant products in best price from certified Chinese Oil Grinding Machine, Cement Processing China Clinker Grinding Plant, Clinker Grinding Plant
احصل على السعر
Shanghai Clirik Machinery Co., Ltd.
Showroom. Workshop. SHANGHAI CLIRIK MACHINERY CO., LTD located in PUDONG New district of Shanghai china as a pioneer enterprise, which is specializing in research, grinding the cement clinker nodules to 100% passing 90 μm in a dry circuit.Grinding occurs at the beginning and the end of the cement making process. Cement grinding optimisation ScienceDirect
احصل على السعر
Breakthrough in Clinker Grinding Massachusetts
Finish grinding of clinker and other cement ingredients reduces 25 mm clinker balls to particle sizes optimally ranging from 3 to 30 microns. The European Small Scale Cement Clinker Grinding Plant And Packaging Unit In Cement Factory working principle: The grinding plate rotates under the action of main motor of LM Vertical Small Scale Cement Clinker Grinding Plant And Packaging
احصل على السعر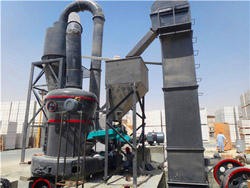
Clinker size and cement grinding GCP Applied Technologies
As a general rule, there should be less than 25% of clinker that is below 1mm in size. Coarse clinker is more of an issue for ball mills. Some cement groups use a Clinker Production. For clinker production, a mixture of clay, limestone, and sand is heated to temperatures near 1500°C. From: Fundamentals and Applications of Supercritical Clinker Production an overview ScienceDirect Topics
احصل على السعر
clinker grinding mills crushing plant
Published Jun 30, 2023 + Follow Clinker grinding mills are an essential part of cement manufacturing plants, where the clinker, a key ingredient in cement production, is ground In 2017 China Resources operated 42 clinker production lines and 91 grinding plants across seven Chinese Provinces, predominantly in the far south and north east of the country. With a total capacity of 79.3Mt/yr, it is smaller than Cemex and UltraTech Cement.Global Cement Top 100 Report 2017 2018
احصل على السعر
Mini Cement Plant, Small Cement Plant 50
Plant Capacity: 50 MT/Day. Plant & Machinery: about 117155 dollars. Working Capital: about 103208 dollars. Total Capital Investment: about 348675 dollars. Return: 23.00%. Break Even: 63.00%. Start Your Mini The three sources are relatively consistent, with the largest portion being consumed in the cement processing stage (grinding the clinker and packaging the cement). This stage is responsible for 40% of the total electricity consumption. The clinker production and raw material preparation both consume roughly 30% of the total electricity each.Industrial production of recycled cement: energy
احصل على السعر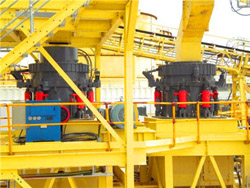
Everything you need to know about clinker/cement Grinding
Previous Post Next Post Contents Everything you need to know about clinker/cement Grinding if You read and understand this article,you will be ready to be a cement grinding area manager. FEED AND FEED SYSTEM Feed Temperature Plants with satellite coolers have high clinker temperatures: e.g. Cumarebo, Oujda.. Exit satellite cooler 200 Three integrated plants share a capacity of 4.1Mt/yr and a single 0.5Mt/yr grinding plant brings the national total to 4.6Mt/yr. It is Cemex Hrvatska’s smallest cement plant and is currently mothballed due to poor market demand. It has a 1180t/day (0.4Mt/yr) KHD four-stage preheater kiln with no calciner, one main burner and a ClaudiusCement in central and eastern EU Member States Global
احصل على السعر
What Equipment is Used for Cement Manufacturing? Prater
Because raw coal is still used in cement manufacturing, equipment that can grind coal onsite is necessary for most cement plants. As with the actual milling of cement, manufacturing equipment used to break down the coal requires mechanisms with airlock capabilities. These must be able to handle capacities from 10-100 tons hourly.2. Grinding occurs at the beginning and the end of the cement making process. Approximately 1.5 tonnes of raw materials are required to produce 1 tonne of finished cement. The electrical energy consumed in the cement making process is in order of 110 kWh/tonne and about 30% of which is used for the raw materials preparation and Cement Grinding Optimization PDF SlideShare
احصل على السعر
Ball Mill Grinding Process Handbook PDF Mill (Grinding)
f HeidelbergCement Group Guidance Paper Edition: 2. Ball Mill Grinding Process Handbook Valid as of: . Feed is pushing the material through the mill, If mill throughput increases: retention. time decreases. Retention time will also depend on L/D ratio of mill. Fluoroscein Tracer test:The Kunda Nordic Tsement plant produced its last clinker in early 2020. It made 571,000t of cement in 2019, its last full year of clinker manufacturing. Akmenés Cementas is the smallest producer. It is partly owned by Germany’s Schwenk Zement (34%) and by HeidelbergCement (8.65%). It also operates a 0.5Mt/yr slag grinding plant inCement in Northern Europe Global Cement
احصل على السعر
Cement Plant Clinker Grinding Plant Manufacturer from
View All Products. LAXMI ENGINEERS. G- 588- B, 2nd Phase, M. I. A., Road No. 8. Basni, Jodhpur 342005, Rajasthan, India. Corporate Video Corporate Brochure. Manufacturer of Cement Plant Clinker Grinding Plant, White Cement Grinding Plant, Automatic Cement Grinding Plant and Mini Cement Plant offered by LAXMI ENGINEERS, Jodhpur, Rajasthan.There is potential to optimise conventional cement clinker grinding circuits and in the last decade significant progress has been achieved. The increasing demand for “finer cement” products(PDF) Cement grinding optimisation ResearchGate
احصل على السعر
Our Process Wonder Cement
Wonder Cement's plant features a 75-meter-long, 5-meter diameter rotary kiln supplied by Polysius Thyssenkrupp of Germany for manufacturing clinker. Raw materials are finely ground and burned in Wonder Cement's plant features a 75-meter-long, 5-meter diameter rotary kiln supplied by Polysius Thyssenkrupp of Germany for manufacturing clinker. Raw materials are finely ground and burned in the kiln, reaching a temperature of 1400-1450℃ in the burning zone with a residence time of 15 minutes.Our Process Wonder Cement
احصل على السعر
Cement Mill Ball Mill Dynamics PDF Mill (Grinding
Note that some plants make a very fine yet seemingly hard to grind clinker. The researchers have observed that a high proportion of big alite crystals can be found in the fine sizes, in these cases. On the other hand for fine grinding (> 3,000 blaine), the main factors become: 1) alite size, as before 2) C2S content,as before 3) grinding aidThe cement industry includes energy-intensive processes, e.g., clinker rotary kilns and clinker grate coolers. Clinker is obtained through chemical and physical reactions in a rotary kiln from raw meal; these reactions also involve combustion processes. The grate cooler is located downstream of the clinker rotary kiln with the purpose of Advanced Process Control for Clinker Rotary Kiln and Grate
احصل على السعر
A comparative analysis of steel and alumina balls in fine
Fig. 2 shows the timewise evolution of the cumulative PSD experimentally obtained from the laboratory batch ball mill with different single ball sizes (i.e., d B = 20, 30, and 40 mm) using steel balls and alumina balls. As milling progressed and finer particles were generated by breakage, the PSD shifted to the left monotonically even in the fine Grinding of cement clinker and granulated blast furnace slag in roller grinding mills (vertical airswept grinding mills) is a technology introduced by Loesche. The first use of a Loesche mill, with a grinding track diameter of only 1.1 metres, was used as long ago as 1935. However, the breakthrough in grinding this type of material on the vertical2 µm 5 µm Loesche
احصل على السعر
Energy-Efficient Technologies in Cement Grinding IntechOpen
The energy consumption of the total grinding plant can be reduced by 20–30 % for cement clinker and 30–40 % for other raw materials. The overall grinding circuit efficiency and stability are improved. The maintenance cost of the ball mill is reduced as the lifetime of grinding media and partition grates is extended. 2.5.Large clinker nodules (Figure 2) are difficult to cool, transport and grind into cement. Clinker should ideally have a smaller average nodule size and a narrow nodule size range. More uniformly sized clinker is more evenly distributed into the cooler and has more consistent bed porosity, which enables more stable cooler and kiln operation.Better and cheaper cement: Optimising the right clinker
احصل على السعر
Cement Grinding Optimization PDF Mill (Grinding)
This chemical reaction occurs at. high temperature in a rotary kiln, grinding the cement clinker nodules to 100%. passing 90 microns in a dry circuit. 2. 2. Grinding occurs at the beginning and the end of the cement making process. Approximately 1.5 tonnes of raw materials are required to produce 1 tonne of.
احصل على السعر