
Modeling and simulation of continuous open circuit dry
The work analyzes how confidently one can predict continuous milling in a dry open-circuit pilot-scale operating under a wide range of feed rates, mill speeds, An alternative to overcome these difficulties is intelligent controls, such as the artificial neural network model predictive control (NNMPC). This study aimed to Modeling and simulation of continuous open circuit dry grinding
احصل على السعر
(PDF) Grinding Media in Ball Mills-A Review
A comparison of the grinding media is given together with the knowledge gaps that still need to be bridged to improve the quality and performance of grinding media used in ball mills.A mineralogy, rheology, and energy consumption-based experimental characterization of chalcopyrite ball mill grinding processes, in both batch and continuous Experimental characterization of chalcopyrite ball mill grinding
احصل على السعر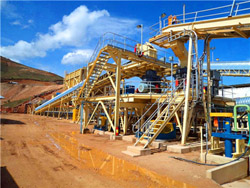
Analysis of holdups in continuous ball mills ResearchGate
Analysis of holdups in continuous ball mills February 2013 Powder Technology DOI: 10.1016/j.powtec.2012.10.053 Authors: Shinichiro Nomura Abstract A Tumbling ball mills or ball mills are most widely used in both wet and dry systems, in batch and continuous operations, and on a small and large scale. Grinding elements in ball Ball Mill an overview ScienceDirect Topics
احصل على السعر
A Review of the Grinding Media in Ball Mills for Mineral
Kelsall et al. investigated the influence of grinding media density on the grinding behaviour of a small amount of quartz in calcite in a continuous ball mill using Oliveira, A.L.; Tavares, L.M. Modeling and simulation of continuous open circuit dry grinding in a pilot-scale ball mill using Austin’s and Nomura’s models. Powder Technol. 2018,340,77–87. [ Google Optimization of Solids Concentration in Iron Ore
احصل على السعر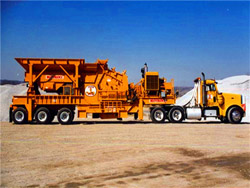
An analysis of fine dry grinding in ball mills ScienceDirect
Abstract. The kinetics of dry grinding of several cement clinkers and two coals were investigated in a laboratory tumbling ball mill. The kinetic process is first-order velocity and increased grinding media surface area insure much finer grind of the processed material. The HSA Attritor is generally used in a continuous mode. The material is charged into the mill at the top by a pre-set rate feeder and discharged out the lower side of the grinding tank. HSA Series Attritors are generally used for finer feedAttrition Dry Milling In Continuous And Batch Modes
احصل على السعر
Ball Mill, Construction, Working Principle,
The ball mill may be operated in a batch or continuous fashion, wet or dry. In a continuously operated mill, as shown in the diagram, the outlet is normally covered with a coarse screen to prevent the escape CERAMIC LINED BALL MILL. Ball Mills can be supplied with either ceramic or rubber linings for wet or dry grinding, for continuous or batch type operation, in sizes from 15″ x 21″ to 8′ x 12′. High density ceramic linings of uniform hardness male possible thinner linings and greater and more effective grinding volume.Ball Mills 911 Metallurgist
احصل على السعر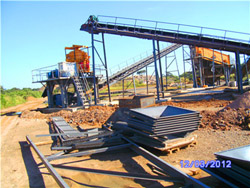
A study on the specific rate of breakage of cement materials
The specific rate of breakage (S i) in the widely accepted first-order expression of grinding rate is one of the important factors required to evaluate a grinding process, particularly for the initial grinding stage in various mill types.In this study, the effects of ball diameter and feed size on the specific rate of breakage were investigated on Impact of the powder flow behavior on continuous fine grinding in dry operated stirred media mills. Miner. Eng. (2018) as grinding aids in the dry grinding of calcite to micronized sizes using a laboratory-scale stirred ball mill and compared them with pure and commercial grinding aids. The test results were evaluated in terms of productGrinding aids for dry fine grinding processes ScienceDirect
احصل على السعر
Ball Mills, Pebble Mills, Material Processing Mills Hatboro
Ball Mills, Pebble Mills, Material Processing Mills: For more than a century, Patterson has been the industry leading manufacturer of wet and dry grinding mills for size reduction or dispersal. Patterson’s ball, pebble and rod mills are built to last. We are still filling parts requests for mills sold over 60 years ago. Patterson mills are available in a wide variety Abstract and Figures. This dissertation focuses on the determination of the selection function parameters alpha, a, mu, and lambda together with the exponent factors eta and ksi describing the(PDF) Effect of ball size distribution on milling parameters
احصل على السعر
Scale-up procedure for continuous grinding mill design
International Journal of Mineral Processing, 7 (1980) 1--31 1 Elsevier Scientific Publishing Company, Amsterdam -- Printed in The Netherlands SCALE-UP PROCEDURE FOR CONTINUOUS GRINDING MILL DESIGN USING POPULATION BALANCE MODELS J.A. HERBST and D.W. FUERSTENAU Department of Dry ball mill is a grinding equipment that uses dry ball milling process to grind materials. Different from the wet ball mill, the dry ball mill does not need to add water when performing the grinding operation, only relying on the impact and crushing effect of the grinding media on the material to grind the material.. The finished material of the dry grinding ball mill is Dry Ball Mill for Sale Buy Dry Grinding Ball Mill with Best Price
احصل على السعر
(PDF) Kinetics of Fine Wet Grinding in a Laboratory Ball Mill
On the other hand, dry ball milling tests were carried out in a laboratory ball mill having a 20 cm internal diameter and 5776 cm 3 volume (Figure 3(b)) with charge of 5475 g steel ball mixturesThe dry mill had a chamber with internal dimensions (D x H) of 30.5 cm × 30.5 cm that amounts to a volume of around 22 l (Fig. 2 a.). The rotational speed of the ball mill was fixed at 70 rpm. A continuous ball charge was used, to simulate the most effective grinding per time [47]. The charge of balls contained 50, 25, and 540 steel sphericalEffect of duration and type of grinding on the particle size
احصل على السعر
Simulation of the grinding of coarse/fine ScienceDirect
Grinding of a coarse fraction (10 × 14 mesh) of each of the three material systems: quartz, dolomite and limestone in a ball mill in the presence of a fine fraction (− 100 mesh) of the same material postulates an important phenomenon. This study shows that the three material systems, ground in a ball mill, behave similarly, i.e., theKeywords: iron ore; ball mill; modeling; simulation; population balance model; slurry density 1. Introduction It has been well over half a century since Austin and Gardner [1], followed by Reid [2], applied the concept of first-order breakage kinetics to steady-state continuous grinding in a mill. The grindingOptimization of Solids Concentration in Iron Ore Ball
احصل على السعر
Continuous grinding in a small wet ball mill. Part V. A study
DOI: 10.1016/0032-5910(73)80065-8 Corpus ID: 95763965; Continuous grinding in a small wet ball mill. Part V. A study of the influence of media shape @article{Kelsall1973ContinuousGI, title={Continuous grinding in a small wet ball mill.Important advances have been made in the last 60 years or so in the modeling of ball mills using mathematical formulas and models. One approach that has gained popularity is the population balance model, in particular, when coupled to the specific breakage rate function. The paper demonstrates the application of this methodology to Optimization of Solids Concentration in Iron Ore Ball Milling
احصل على السعر
Grinding aids for dry fine grinding processes ScienceDirect
Impact of TEA on the grinding of clinker in vibration disc and tumbling ball mill, when grinding with mill parameter that lead to identical Blaine values without any Impact of the powder flow behavior on continuous fine grinding in dry operated stirred media mills. Miner. Eng., 128 (2018), pp. 215-223. View PDF View article View in ScopusStirred media mills are used by the mining industry for ultrafine grinding to enhance liberation, and to decrease particle sizes of industrial minerals to tailor functional properties. This review describes stirred media mill technologies and operating principles, and summarises stress intensity theory which can be used for selecting efficient Stirred media mills in the mining industry: Material
احصل على السعر
Ball Mill Principle, Construction, Working, and More Soln
Ball mills are used primarily for single-stage fine grinding, regrinding, and as the second stage in two-stage grinding circuits. According to the need ball mill can be either for wet or dry designs. Ball mills have been designed in standard sizes of the final products between 0.074 mm and 0.4 mm in diameter.2 天之前We are your first choice for the grinding of dry products! Products & Solutions Dry Grinding. From A (activated carbon) to Z (zinc oxide) -. we offer the right mill for your product. Our extensive experience and wide range of mills are available for the fine cutting, fine grinding and ultra-fine grinding of dry products of all desired finenesses.Dry Grinding NETZSCH Grinding & Dispersing
احصل على السعر
What is a ball mill? What are its uses and advantages?
Ball Mill Features. Continuous operation and large capacity. High utilize ratio and low consumption of modifying agent. With the function of modifying and dispersion, it fits for various
احصل على السعر