
Iron Ore Processing, General SpringerLink
First Online: 20 October 2022 178 Accesses Abstract Iron ore resource has its own peculiar mineral characteristics requiring suitable processing or beneficiation to produce quality Making iron and steel from iron ore requires a long process of mining, crushing, separating, concentrating, mixing, agglomeration (sintering and pelletizing), Iron Ore Processing, General Springer
احصل على السعر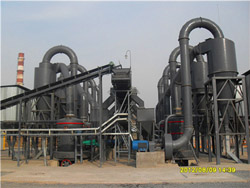
Iron Ore Processing an overview ScienceDirect Topics
Current practice of washing iron ore before it is processed for extractive metallurgical operation results in three products, coarse ore lumps with sizes in the range 10-80 mm, Iron Ore production in the Pilbara. Activities involved in finding, mining and processing iron ore at our Pilbara operations have been simplified in the following Iron Ore production in the Pilbara Rio Tinto
احصل على السعر
Life cycle assessment of iron ore mining and processing
Mining of iron ore is a highly capital and energy-intensive process. Life cycle assessment of the mining and mineral processing of iron ore in Australia was carried out As iron and steel production has become concentrated into ever larger centers of production, and steel has become an internationally traded commodity, so iron Iron ore extraction techniques ScienceDirect
احصل على السعر
The Composition and Performance of Iron Ore Tailings in
Iron ore tailings (IOTs) are byproducts of the iron mining industry that have gained significant attention in recent years due to their potential for comprehensive Six steps to process iron ore. 1. Screening. We recommend that you begin by screening the iron ore to separate fine particles below the crusher’s CSS before the crushing stage. A static screen is used to divert the fine particles for crushing. This step prevents overloading the crusher and increases its efficiency.The six main steps of iron ore processing Multotec
احصل على السعر
Iron ore sintering ScienceDirect
Abstract. Sintering is the most economic and widely used agglomeration process to prepare iron ore fines for blast furnace use. In this chapter, the sintering process is first described to identify the key steps of the process, that is, granulation and thermal densification. Discussion is then focused on the effect of the chemical, physicalIron ore tailings (IOTs) are a form of solid waste produced during the beneficiation process of iron ore concentrate. In this paper, iron recovery from IOTs was studied at different points during a process Minerals Free Full-Text Recovering Iron from
احصل على السعر
Collecting Agent–Mineral Interactions in the Reverse Flotation of Iron
Froth flotation has been widely used in upgrading iron ores. Iron ore flotation can be performed in two technical routes: direct flotation of iron oxides and reverse flotation of gangue minerals with depression of iron oxides. Nowadays, reverse flotation is the most commonly used route in iron ore flotation. This review is focused on the reverse Mining of iron ore is a highly capital and energy-intensive process. Life cycle assessment of the mining and mineral processing of iron ore in Australia was carried out in this chapter using(PDF) Life cycle assessment of iron ore mining and processing
احصل على السعر
Life cycle assessment of iron ore mining and processing
The extraction of iron ore involves surface (open-pit) or underground mining techniques (please refer to Chapter 7 (Stace, 2014) on Iron Ore Extraction Techniques).The LCA boundary used in this study is shown in Fig. 21.4.The mining method selected depends on a variety of factors, including the nature and location of the deposit, and the size, In pelletizing, the finely ground iron ore is rolled to pellets before firing in a kiln or on a grate machine. 1.1.1.4. Blast Furnace Process in Brief1.1.1.4.1. Blast Furnace Process for Integrated Steelmaking pelletizing is another widely used process to agglomerate the iron ore. Sinter plants are usually located near the blast furnaceIronmaking ScienceDirect
احصل على السعر
Low carbon ironmaking technologies: an European approach
The Finmet process developed jointly by Fior de Venezuela and Voest-Alpine Industrieanlagenbau GmbH & Co (now Primetals Technologies) on the basis of the FIOR (Fluidized bed Iron Ore Reduction) is again a gas based direct reduction process of fine iron ores (less than 12 mm, incl. 30% <0.15 mm) in a four-stage fluidizing bed The Brucutu iron ore mine (Minas Gerais, Brazil) is Vale‘s largest iron producing operation achieving around 21 million tons per annum. Evaluation of flotation performance is of high importance as even small gains can lead to large monetary benefits. Cell-by-cell samples of the froth products, selected feed and pulp-products were Minerals Free Full-Text Process Evaluation of an Iron Ore
احصل على السعر
What equipment is used in iron ore crusher? LinkedIn
Here are some common types of equipment used in iron ore crushing: 1. Jaw Crusher: This is a primary crusher that is used for coarse crushing. It has a fixed jaw plate and a movable jaw plate, andThe jaw crusher is generally used in the crushing process of iron ore. The jaw crusher is a traditional and reliable coarse crushing equipment, and its application range is extremely wide. The Challenges and opportunities in the iron ore
احصل على السعر
What equipment is needed for iron ore mines LinkedIn
1.Excavators: These are large machines used to dig and remove the overburden, or top layer of soil and rock, to access the iron ore deposit. 2.Haul trucks: These are heavy-duty trucks used toIn iron ore granulation process, the variables are numerous and complex, the particles show irregular . discrete motion, machine at the Fukuyama plant as early a s 1988 120,121).(PDF) Iron Ore Granulation for Sinter Production:
احصل على السعر
Multi-objective Optimization of Integrated Iron Ore Sintering Process
The steps involved in the iron ore sintering process is shown in Fig. 1.Various raw materials used in sintering viz. iron ore fines, fluxes, solid fuel and steel plant reverts are blended in a specific proportion as per the desired chemical composition of sinter and stockpiled in an open yard.A technology assessment checklist that investors should consider when making a new pellet plant investment decision is presented. Schematic of the straight grate pelletizing process. Thermal(PDF) GUIDELINES FOR SELECTING PELLET PLANT TECHNOLOGY
احصل على السعر
Introduction: Overview of the global iron ore industry
Turning to iron ore exports and imports, the tonnages are summarized in Table 1.1 for 2012 and 2018 (Australian Department of Industry, Science, Energy and Resources, 2021; US Geological Survey, 2020; United National Conference on Trade and Development (UNCTAD), 2021).As shown in Fig. 1.3, China is the largest iron ore The blast furnace uses coke, iron ore and limestone to produce pig iron. Coal traditionally has been a key part of the coke-making process. The coal is crushed and ground into a powder and then charged into an oven where it is heated to approximately 1800°F in the absence of oxygen. As the oven is heated, the coal begins to melt so most of theSteel Production American Iron and Steel Institute
احصل على السعر
(PDF) An Overview of the Reduction-Smelting Process of Iron
A laboratory experiment was carried out to extract iron from oolitic iron ore by a deep reduction and magnetic separation technique. The raw coal with fixed carbon of 66. 54% was used as theThe quality of Indian iron ore resources is generally good with high iron content and high percentage of lumpy ore. More than 85% of the hematite ore reserves are of medium- to high-grade (+62% Fe) and are directly used in blast furnace and in direct-reduced iron (DRI) plants in the form of sized lump ore, agglomerated sinter, and Iron ore beneficiation: an overview ScienceDirect
احصل على السعر