
A comparative study of pellets, sinter and mixed ferrous
A clear difference in the present phases between the sinter and pellets is observed (Figures 13 (d) and 14). In the pellet region, along with the dense reduced iron layer, a slag rich in Hot metal production using sinter and pellets in the blast furnace is compared, considering aspects like; blast furnace productivity, (PDF) COMPARISON OF SINTER AND PELLET
احصل على السعر
COMPARISON OF SINTER AND PELLET USAGE IN AN
17 小时之前Hot metal production using sinter and pellets in the blast furnace is compared, considering aspects like; blast furnace productivity, environmental performance, solid The velocity of pellets is always larger than that of sinter, and the velocity difference between pellets and sinter also become larger which are 0.53 m/s, 0.63 m/s, Effects of pellet ratio on the burden movement and
احصل على السعر
Quantitative XRD analysis and evaluation of iron ore, sinter, and pellets
Powder X-ray diffraction (XRD) is increasingly being used for the characterization of iron ore, sinter, and pellets thanks to the continuing developments in It is found that lump ore has lowest reduction rate in all test conditions, and at lower temperatures iron ore pellets reduce faster than sinter, and this is reversed at Reduction of Iron Ore Pellets, Sinter, and Lump Ore under
احصل على السعر
A comparative study of pellets, sinter and mixed
PDF Physicochemical behaviour of the pellets, sinters and its mixture (60% pellets: 40% sinter) is investigated by a series of smelting and quenching Find, read and cite all the researchIn this study, the behavior of reduction, softening and melting of a lump ore, an acid pellet, and a sinter was characterized by softening and melting (S&M) Microstructure and Porosity Evolution During the Reduction
احصل على السعر
Advances in Sintering and Pellet Technology MDPI
Agglomeration processes are typically of three types: pelletizing, briquetting, and sintering. Sintering is a manufacturing technology to make a wide variety of engineering materials, ceramic and The principle difference between sinter and pellets arises between sinter and BF pellets are the total iron (Fe) content, the total acid gangue (SiO 2 + Al 2 O 3COMPARISON OF SINTER AND PELLET USAGE IN AN
احصل على السعر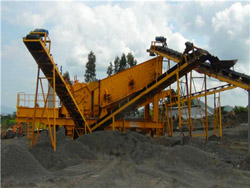
Advances in Sintering and Pellet Technology MDPI
These differences mainly stemmed from the influence of calcium-containing substances in fluxed pellets. Herein, the theoretical investigation discovered the calcium-containing substances from fluxed In the above research foundation of the movement difference between sinter and pellets, the movement behavior of mixed burden with different pellet ratios is further studied. Fig. 6 presents the particle flow trajectory of the mixed burden with different pellet ratios. It can be seen that the whole particle flow is relatively concentrated whenEffects of pellet ratio on the burden movement and
احصل على السعر
Quantitative XRD analysis and evaluation of iron ore, sinter, and pellets
For sinters, ongoing studies have identified differences according to different blend compositions and also differences between sinter size fractions, to be discussed later. Fig. 3.7 shows the differences between different clusters of sinter samples as small spheres of different colors. The biggest differences between samples are manifestedFurthermore, at 10 pct contraction, a pseudo-globular wüstite structure interspersed with slag was observed for the pellet and sinter cores. At 50 pct contraction, the previous structure coalesced to form a globular shape wüstite in a well-connected slag matrix. self-fluxed pellet, and sinter. The maximum difference between T D and T E2Microstructure and Porosity Evolution During the Reduction
احصل على السعر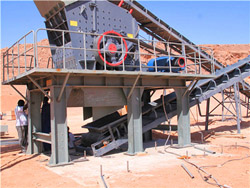
Measurement and simulation validation of DEM parameters of pellet
There is an obvious difference between the friction coefficients of the pellet and sinter, which had been measured or calibrated by different researchers [12, 13,16,19,20]. In order to eliminateThere have been studies about the low-temperature reduction degradation characteristics of pellets, sinter, and lump ore, [] as well as the softening, shrinking, and melting reduction behavior of all charge materials or just part of them. [3-9]Even though some research has considered all iron-bearing materials (sinter, iron ore pellets, and Reduction of Iron Ore Pellets, Sinter, and Lump Ore under
احصل على السعر
Mixed burden softening-melting property optimization
The use of high basicity sinter with high-silica fluxed pellet is the direction of development of high proportion pellets suitable for our resource characteristics [9,10]. Many scholars have studied the differences between acid and fluxed pellets, and softening-melting behavior of high proportion pellets in blast furnace.study. Jagannath found that there was only a tiny difference between the metallurgical performances of limestone fluxed pellet and calcium lime fluxed pellet with basicity of 0.2.18) The hydrated lime may be more suitable for preparation of basic pellets as it can provide abundant CaO in the indura-Utilization of Hydrated Lime as Binder and Fluxing Agent
احصل على السعر
Sintering and Pelletizing TON
Ensure your plant’s high performance and profitability while lowering investment and operating costs with our agglomeration technologies. Our innovative sintering and pelletizing solutions are based on over 60 years’ The expediency of applying the test methods for sinter and pellets to determine the mechanical strength of blast-furnace briquettes is considered. Based on numerical modeling, the behaviors of pellets and briquettes under shock and abrasive loads in a rotating drum, static compressive loads, and when dropped from a height are Tests of Briquettes for Mechanical Strength SpringerLink
احصل على السعر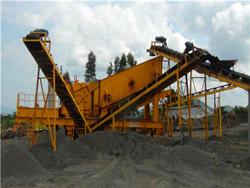
A comparative study of pellets, sinter and mixed
In mixed bed (upto 1505°C), the interaction between the pellet and sinter is limited to the interface only. The sinter slag is observed to control the melting and dripping properties of the mixedSinter quality begins with the mined iron ore and the proper selection and mixing of the raw materials. Inhomogeneous raw mix can affect permeability and cause an increase in fuel consumption. During the iron ore sintering process in iron and steel manufacturing, an online analyzer can be used to determine the elemental composition Sintering: A Step Between Mining Iron Ore and Steelmaking
احصل على السعر
Iron ore pricing explained Fastmarkets
Sinter fines and lumps make up the bulk of the seaborne iron ore market, and are the products most frequently traded on a spot basis, so daily pricing is used for the key 62% Fe, 58% Fe and 65% Fe fines, and lump premium references. By contrast, the beneficiated ore segment comprising pellet and concentrate is smaller in terms of sinter, 20% lump ore, and 15% pellets is found to have the best results (Hsieh and Liu 1998 ). Pal et al. 1998,studied the softening temperature of a series(PDF) Iron Ore Sintering: Process ResearchGate
احصل على السعر
Effect of Iron Ore Pellet Size on Metallurgical Properties
Iron ore pellets are small and hard spherical particles agglomerated from a fine iron ore concentrate. They are used in the blast furnace process to produce hot metal. The diameter of blast furnace pellets is usually between 8 and 16 mm. In this study, a batch of magnesia iron ore pellets was first sieved into particle sizes of 8–10 mm, 10–12.7 mm, The lump ore from Azul (47.7% in the overall sample) and the pellets (50.9%) have a manganese content considered good for the process. The difference in manganese content reaches 3.2%. The lump ore from Azul has a Mn/Fe ratio of 13.3, while that of the pellets is 6.8.A geometallurgical comparison between lump ore and pellets
احصل على السعر
the choice of pellets in a mixed blast furnacethe choice
The experimental blast furnace has been quenchedtwice on olivine pellets and once on a KPBA type pellet. Some differences in melting charac-teristics can be observed. 3 RESULTS. 3.1 Experimental Blast Furnace. Some operational results from the trials are gathered in Table 4. Table 4 Process parameters in pellet-sinter trials in the For comparison, the reduction-disintegration indices of sinters with a basicity (CaO+MgO)/(Al 2 O 3 + SiO 2) of 1.2, 1.4, and 1.6, obtained from the PJSC “NLMK” conventional charge, were simultaneously evaluated according to the same standard (Table 3).The reduction-disintegration index of the sludge brexes is comparable to that of a Sintering and Briquetting Synergy in Blast Furnace Smelting
احصل على السعر