
(PDF) Grinding in Ball Mills: Modeling and Process
The paper presents an overview of the current methodology and practice in modeling and control of the grinding process in industrial geometrical lifter structure and to improve the performance of the ball mill. Keywords: ball mill; DEM; height-width ratio; rectangular lifter; number of lifter. 1 Study on the Performance of Ball Mill with Liner
احصل على السعر
[PDF] Grinding in Ball Mills: Modeling and Process Control
Materials Science 2022 7th International Conference on Mathematics 2022 The paper presents advanced technologies and equipment for metal powder PDF In the early 1990s the discrete element method (DEM) was used for the first time to simulate media motion in tumbling (PDF) A Review of Advanced Ball Mill Modelling
احصل على السعر
Ball milling: a green technology for the preparation and
DOI: 10.1039/c8na00238j. rsc.li/nanoscale-advances. Ball milling is a simple, fast, cost-effective green technology with enormous potential. One of the most interesting Introduction. High-energy ball milling (HEBM) is a treatment of powders, which uses the action of the milling media to mix, disperse, activate and form composite structures [ 1, 2, 3, 4 ]. The milling Materials Development Using High-Energy Ball
احصل على السعر
VWRUDJHGHYLFHV IOPscience
Ball milling is one of the most profitable and cost-effective processes of electrode material processing. However, in most of the ball milling research, the focal THE PERFECT BALL MILL FOR EVERY APPLICATION 04 05 RE-INVENTING BALL MILL TECHNOLOGY MIXER MILL MM 500 06 09 Dear Readers, Verder Scientific Customer Magazine Issue 44 BALL MILLS
احصل على السعر
[2311.13571] Ball Mill Fault Prediction Based on Deep
Download PDF Abstract: Ball mills play a critical role in modern mining operations, making their bearing failures a significant concern due to the potential loss of A numerical dynamic-mechanical model of a planetary ball-mill is developed to study the dependence of process efficiency on milling parameters like ball size and number, jar geometry and velocity(PDF) DESIGN AND FABRICATION OF MINI BALL
احصل على السعر
[PDF] Grinding in Ball Mills: Modeling and Process Control
An overview of the current methodology and practice in modeling and control of the grinding process in industrial ball mills is presented. Abstract The paper presents an overview of the current methodology and practice in modeling and control of the grinding process in industrial ball mills. Basic kinetic and energy models of the grinding Ball mill is an operating unit used to grind various types of solid materials into finer particle sizes. The purpose of this study was to determine the best variation of operating conditions of(PDF) DESIGN AND FABRICATION OF MINI BALL MILL.
احصل على السعر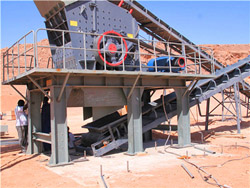
Ball milling: a green technology for the preparation and
The ball mill Ball milling is a mechanical technique widely used to grind powders into ne particles and blend materials.18 Being an environmentally-friendly, cost-effective technique, it has found wide application in industry all over the world. Since this mini-review mainly focuses on the conditions applied for the prep-Ball milling is a simple, fast, cost-effective green technology with enormous potential. One of the most interesting applications of this technology in the field of cellulose is the preparation and the chemical modification of cellulose nanocrystals and nanofibers. Although a number of studies have been repo Recent Review Articles Nanoscale Advances Most Popular Ball milling: a green technology for the preparation and
احصل على السعر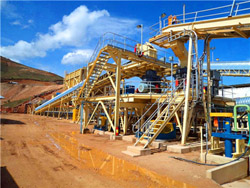
MODULE #5: FUNCTIONAL PERFOMANCE OF BALL
In a ball mill circuit, the "output" can be defined as the production rate of fines of the circuit. As for any output, ball mill circuit output is a function of both its inputs and efficiencies. There are two "inputs" to a ball mill circuit: the ore fed to the circuit and the power delivered by the grinding mill.Attrition: Reduced the size of the materials when they colloid by heavy weight (Ball). Construction: The ball mill grinder consists following Parts: Cylinder: cylinder is made of a hollow metal that moves about its horizontal axis. the cylinder can be made of porcelain, metal, and rubber. the length of the cylinder slightly higher than its diameter.Ball Mill; Principle, Working, and Construction » Pharmaguddu
احصل على السعر
EFFECTS OF GRINDING MEDIA SHAPES ON BALL MILL
SHAPES ON BALL MILL PERFORMANCE Niyoshaka Nistlaba Stanley Lameck A dissertation submitted to the Faculty of Engineering and The Built Environment, University of the Witwatersrand, Johannesburg, in fulfilment of the requirements for the degree of Master of Science in Engineeringmill (ball or vertical) to produce ‘raw meal’ under a strict quality control of the material chemistry. Hot flue gases coming from the rotary kiln, which is in the opposite direction with the material flow, preheat the powdered raw meal at the preheater tower before it finally enters the kiln. In these preheater cyclones, raw8VLQJ$VSHQ 3OXV6LPXODWRU IOPscience
احصل على السعر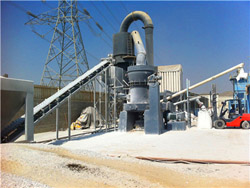
Study on the Performance of Ball Mill with Liner
2.3 Ball Mill Model The main structure of the ball mill is composed of three parts, namely the feed inlet, the cylinder part (work bin), and the discharge port. Figure 2(a) shows the structural model of a ball mill. In the mill cylinder part, there are lifters for turning over the particles. The quartz sand particles enter the cylinder through aMechanochemical technique aims to strike a balance between defect formation via ball milling and size adjustment of a solid grain to nanoscale (<1000 nm) (Ullah et al., 2014).During the process, a high-energy mill is employed and a specific powder charge is placed along with a milling medium (Lin et al., 2017).The kinetic energy Ball milling as a mechanochemical technology for fabrication
احصل على السعر
BALL MILLS Ball mill optimisation holzinger
Ball mills and grinding tools Cement ball mills are typically two-chamber mills (Figure 2), where the first chamber has larger media with lifting liners installed, providing the coarse grinding stage, whereas, in the second chamber, medium and fine grinding is carried out with smaller media and classifying liners.High-energy ball milling (HEBM) of powders is a complex process involving mixing, morphology changes, generation and evolution of defects of the crystalline lattice, and formation of new phases. This review is dedicated to the memory of our colleague, Prof. Michail A. Korchagin (1946–2021), and aims to highlight his works on the synthesis of Materials Development Using High-Energy Ball Milling: A
احصل على السعر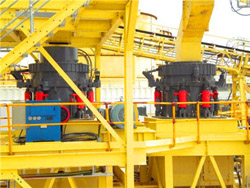
RANCANG BANGUN BALL MILL DARI BAJA DIAMETER
Gambar. 2. Mesin ball mill Ball mill digerakkan dengan motor AC 1 fasa dengan daya 0,5 HP dimana dalam tabungnya terdapat bola baja berjumlah 40 buah dengan diameter 20 mm dan sistem transmisi daya menggunakan pulley dan belt. ModifikasiTo predict ball mill grinding behavior using the dis-crete element method, we must first be able to repro-duce the balls’ motion in the ball mill using simula-tions. Kano et al.8) have made it clear that it is possible to reproduce the ball motion when the solid material is also present in a tumbling ball mill without fins by pro-Design Method of Ball Mill by Discrete Element Method
احصل على السعر
Ball Mills 911 Metallurgist
CERAMIC LINED BALL MILL. Ball Mills can be supplied with either ceramic or rubber linings for wet or dry grinding, for continuous or batch type operation, in sizes from 15″ x 21″ to 8′ x 12′. High density ceramic linings of uniform hardness male possible thinner linings and greater and more effective grinding volume.Download. The Planetary Ball Mill PM 100 is a powerful benchtop model with a single grinding station and an easy-to-use counterweight which compensates masses up to 8 kg. It allows for grinding up to 220 ml sample material per batch. The extremely high centrifugal forces of Planetary Ball Mills result in very high pulverization energy and行星式球磨仪PM100--德国RETSCH(莱驰)研磨仪粉碎仪
احصل على السعر
Principle and Application of the Ball End Mill Tool Radius
Common 3-axis CNC milling machines are generally equipped with 2D tool radius compensation (2D-TRC), which can realize TRC function for the contours in three basic planes when flat end mills are used. The 2D-TRC function makes engineers to program according to the actual contour of a part, and avoids over-cut phenomenon. The Planetary Ball Mill PM 100 is a powerful benchtop model with a single grinding station and an easy-to-use counterweight which compensates masses up to 8 kg. It allows for grinding up to 220 ml sample material per batch. The extremely high centrifugal forces of Planetary Ball Mills result in very high pulverization energy and therefore shortPlanetary Ball Mill PM 100 RETSCH highest fineness
احصل على السعر