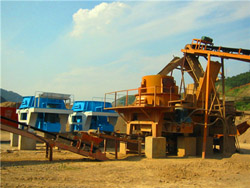
Full article: An overview of alternative raw materials used in cement
Cement production process with waste utilisation areas. Display full size. In stage one, the essential raw materials-limestone, laterite, bauxite, kaolinite, clay, iron ore, sandstone, Low (2005) performed the first comprehensive material flow analysis for concrete, and calculated the amounts of raw material, water, and energy required as Analysis of material flow and consumption in cement production process
احصل على السعر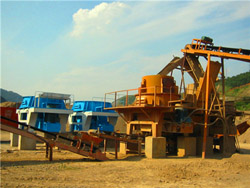
Cement Definition, Composition, Manufacture,
This article surveys the historical development of cement, its manufacture from raw materials, its composition and properties, and the testing of those properties. The focus is on portland cement, but attention Cement manufacturing is a complex process that begins with mining and then grinding raw materials that include limestone and The Cement Manufacturing Process Thermo
احصل على السعر
Cement Production an overview ScienceDirect Topics
Cement production processes can be categorized as dry, semidry, semiwet, and wet processes depending on the handling of raw material before being fed to the rotary kiln. Raw materials are used to produce the main cement elements (Mohsen, 2015) • Quarry The process of obtaining raw materials for cement manufacturing involves mining and quarrying natural materials(PDF) Cement Manufacturing ResearchGate
احصل على السعر
Chapter 4 Cement Manufacturing and Process Control
The cement is now ready for use in construction projects. The flow sheet of cement manufacturing is given in Fig. 4.1. Kiln feed is subjected to succes-sive physical The cradle-to-grave includes four stages: raw material, manufacture, distribution and final disposal. The raw material stage included the manufacturing of raw Production of cement and its environmental impact
احصل على السعر
How Cement Is Made Heidelberg Materials
de The most important raw materials for making cement are limestone, clay, and marl. These are extracted from quarries by blasting or by ripping using heavy There are four stages in the manufacture of portland cement: (1) crushing and grinding the raw materials, (2) blending the materials in the correct proportions, (3) burning the prepared mix in a kiln, and (4) grinding the burned product, known as “ clinker,” together with some 5 percent of gypsum (to control the time of set of the cement). The three processes of Cement Extraction, Processing, Manufacturing Britannica
احصل على السعر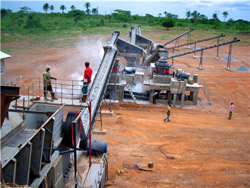
What Is Cement Definition, History, Types
2 天之前Raw Materials of Portland Cement . Calcareous rocks material (CaCO3 > 75% such as limestone, marl, chalk), Argillaceous rocks material (CaCO3 < 40% such as clay and shale), In the dry process mixing of The cement industry is a significant CO 2 emitter mainly due to the calcinations of raw materials and the combustions of fuels. Some measures have been considered to reduce the CO 2 emissions in cement industry, of which alternative raw materials are the most efficient practicing way. In this study, a LCA-based CO 2 Analysis of CO2 Emission for the Cement Manufacturing with Alternative
احصل على السعر
Full article: An overview of alternative raw materials used in cement
Raw materials chemistry. Cement manufacture requires a source of calcium, such as CaCO 3 or CaMg (CO 3) 2, which comprises almost 80–90% of the total and the rest is iron oxide (Fe 2 O 3, Fe 3 O 4), quartz (SiO 2), and clay/bauxite (Al-silicates) (Aïtcin and Flatt Citation 2015; Hewlett Citation 2003; Peray and Waddell Citation 1986).Traces of Na 2 O, K 2 O, concrete, in construction, structural material consisting of a hard, chemically inert particulate substance, known as aggregate (usually sand and gravel), that is bonded together by cement and water. Among the ancient Assyrians and Babylonians, the bonding substance most often used was clay. The Egyptians developed a substance Concrete Definition, Composition, Uses, Types, & Facts
احصل على السعر
Sustainability Free Full-Text Recent Progress in Green Cement
The cement industry is facing numerous challenges in the 21st century due to depleting natural fuel resources, shortage of raw materials, exponentially increasing cement demand and climate linked environmental concerns. Every tonne of ordinary Portland cement (OPC) produced releases an equivalent amount of carbon dioxide to the atmosphere. In this Wet process. Dry Process of Manufacture of Cement: Crushing of limestone and clay in crushers and stored in silos. Grinding of crushed materials and storing in hoppers. Mixing of materials by compressed air in the right proportions to form a raw mix. Burning of raw mix in a rotary kiln to form clinkers.2 Process Of Manufacture Of Cement Civil Giant
احصل على السعر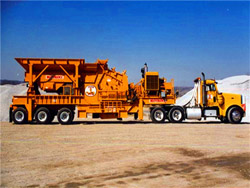
Guidelines for the Selection and Use of Fuels and Raw Materials
Ordinary Portland Cement and blended cements are the most commonly used types of cement. Use of fuels and raw materials in cement manufacture. 10 Cement must conform to the strict building standards set for it. Consequently, the manufacturing process itself must be closely monitored and controlled to obtain clinker and cement that meet theseCo-processing is a thermal treatment process to utilize wastes as resources in the resource intensive industries (RIIs) such as Cement kilns, Thermal Power Plants, Steel Plants, Glass Manufacturing plants, Refractory Manufacture plants, and Lime plants. Wastes get utilized as alternative fuels and raw materials (AFRs) in the RIIs and Co-processing of Wastes as AFRs in Cement Kilns Springer
احصل على السعر
Co-processing of Industrial Waste in Cement Kiln
These by-products can be reused by mixing with raw materials and fed to cement process. Moreover these wastes can be substitute with clinker and can become a composition of final cementThe attention to environmental impacts of cement production has grown fast in recent decades. The cement industry is a significant greenhouse gases emitter mainly due to the calcinations of rawEnvironmental Impacts of Cement Production: A Statistical Analysis
احصل على السعر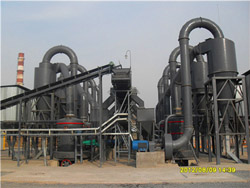
2 Types of Manufacturing of Cement Wet and
Manufacturing of cement is a process that involves several steps, from extracting raw materials to packaging and shipping the final product. In this blog post, we will explain two main processes of cement manufacturing This paper reviews the impact of cement industry towards the global environment and solutions to the problem. The increasing harvesting of raw materials for mounting cement manufacturing causes reduction in quantity of the non-renewable resources such as limestone. The activities linked to harvesting of the resources from Environmental impact of cement production and Solutions:
احصل على السعر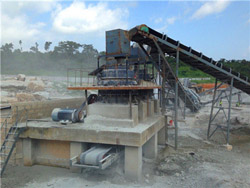
(PDF) Introductory Chapter: Cement Industry ResearchGate
Cement-based materials, such as concrete and mortars, are used in extremely large amounts. For instance, in 2009 concrete production was superior to 10 billion tons.Stage 2: Crusher (grinding) The quarried material is reduced in size by compression and impacted in various mechanical crushers. Crushed rock is reduced in size from 120 cm to between 1.2 and 8 cmFig. 12. Stages in cement production flow chart [43].
احصل على السعر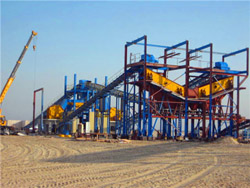
(PDF) THE CEMENT MANUFACTURING PROCESS
THE CEMENT MANUFACTURING PROCESS Prof. Dr Elshafie Ahmed Gad Faculty of Applied Science Chemistry Dept. Portland Cement Portland cement is made by mixing substances containing CaCO3 with substances containing SiO2, Al2O3, Fe2O3 and heating them to a clinker which is subsequently ground to powder and mixed with 2-6 % gypsum Stage of Cement Manufacture. There are six main stages of the cement manufacturing process. Stage 1: Raw Material Extraction/Quarry The raw cement ingredients needed for cement production are limestone (calcium), sand and clay (silicon, aluminum, iron), shale, fly ash, mill scale, and bauxite. The ore rocks are quarried and How Cement is Made Cement Manufacturing Process
احصل على السعر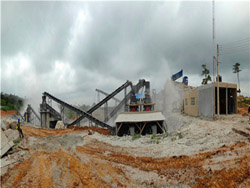
(PDF) Cement Types, Composition, Uses and Advantages of
In cement manufacturing, raw materials of cement are obtained by blasting rock quarries by boring the rock and setting off explosives [2]. ese fragmented rocks are thenThe bulk of the cement industry's environmental burden is from the calcareous source. Calcium is mostly available naturally as limestone (CaCO 3), where almost half of the mass is eventually released as CO 2 during clinker manufacture. Iron (Fe) is the fourth most common element in the Earth's crust surpassed only by oxygen, Sustainable iron-rich cements: Raw material sources and
احصل على السعر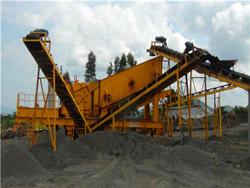
11.6 Portland Cement Manufacturing U.S.
A. Dry Process Kiln -06 B. Raw material unloading -07 C. Raw material piles -08 D. Primary crushing -09 E. Secondary crushing -10 F. Screening -11 Cement raw materials are received with an initial moisture content varying from 1 to more than 50 percent. If the facility uses dry process kilns, this moisture is usually reduced to less than
احصل على السعر