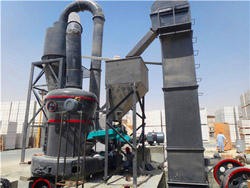
Full article: Evaluation of optimization techniques for
The cement raw mill is the primary piece of equipment used in the modern cement industry for the raw meal production process. As a result, it is critical to investigate the exergy Three raw meals obtained from different cement plants in Spain and Italy (RM1-3) were tested, together with a “synthetic Ca–Si mixture”, SM, composed of a CO2 Carrying Capacities of Cement Raw Meals in Calcium
احصل على السعر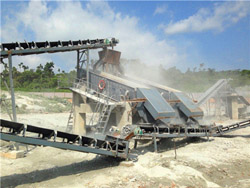
Efficient machine learning model to predict fineness, in a vertical raw
This work aims to develop a soft sensor for raw meal fineness in a vertical roller mill of a cement plant. In previous research, some key indicators of the process Abstract Cement production is one of the most energy-consuming industries in the world, and the grate cooler plays a vital role in cement quality and Energy and thermodynamic analysis of a typical cement
احصل على السعر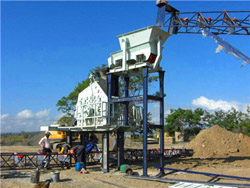
Evaluation of optimization techniques for predicting
The exergy efficiency of the cement raw meal manufacturing process is investigated in this study. The Aspen Plus process model was used for plant modeling Phase evolution and burnability of cement raw meal. Advances in Cement Research 2023, 10,1-11. https://doi/10.1680/jadcr.23.00034; Steve Griffiths, Benjamin K. Sovacool, Carbon Capture in the Cement Industry: Technologies,
احصل على السعر
Influence of raw meal composition on clinker reactivity and cement
The impact of the raw meal composition on the cement performance is summarized in the following conclusions: • The increase of LSF of raw meal causes a During a standard cement manufacturing plant process, the raw meal is converted into clinker in two steps: calcination and clinkering. Calcination needs a Reactivity of calcined cement raw meals for carbonation
احصل على السعر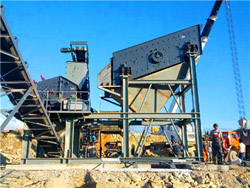
CO2 Carrying Capacities of Cement Raw Meals in Calcium
Calcium looping, CaL, is an emerging CO2 capture technology that is of special interest for use in cement plants, as it offers the possibility of exploiting several energy and material synergies. In this work, the CO2 carrying capacity of calcined raw meal materials for cement plants has been investigated with thermogravimetric equipment in a The bulk of the cement industry's environmental burden is from the calcareous source. Calcium is mostly available naturally as limestone (CaCO 3), where almost half of the mass is eventually released as CO 2 during clinker manufacture. Iron (Fe) is the fourth most common element in the Earth's crust surpassed only by oxygen, Sustainable iron-rich cements: Raw material sources and
احصل على السعر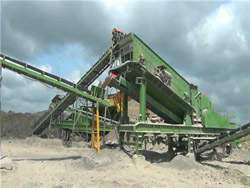
Full-scale investigations of initial deposits formation in a cement
1. Introduction. Cement is the basic ingredient (the binder) of concrete, the most-used manufactured substance on the planet in terms of volume. Portland cement is produced from a mixture of CaO, SiO 2, Al 2 O 3 and Fe 2 O 3-bearing raw materials (typically ground limestone, clay, sand, shale, bauxite and iron ore) in an energy Using the dry-process cement production technology, the 5000 t/d cement plant in China mainly includes raw meal preparation, clinker calcination, and cement production. Clinker calcination is the core step of production, mainly composed of preheater, decomposition furnace, rotary kiln, grate cooler, and other equipment.Energy and thermodynamic analysis of a typical cement
احصل على السعر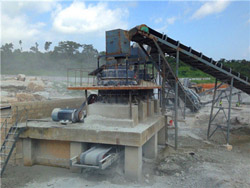
Integrated Calcium Looping System with Circulating
In this work, a Calcium Looping (CaL) configuration for cement plants using two interconnected circulating fluidized bed (CFB) reactors integrated into the clinker production process, is investigated. In the proposed system, the oxy-fired CFB calciner has a dual task: (i) calcining the finer fraction of the raw meal to feed the rotary kiln of the The cement raw mill is the primary piece of equipment used in the modern cement industry for the raw meal production process. As a result, it is critical to investigate the exergy efficiency in a cement raw mill in order to satisfy the need for the design and optimization of the cement plant manufacturing process.Full article: Evaluation of optimization techniques for
احصل على السعر
Decarbonization options for cement production process: A
The conceptual layout of a modern cement production plant is presented in Fig. 1 [8].The production of cement involves the raw material (meal) preparation followed by the pyro-processing step in which the raw meal is heated up to the sintering temperature (higher than 1400 °C) to produce clinker which then is blended with additives (e.g. capture in cement plants19,20 mainly because the same calcium-based raw meal, once it has been calcined, can be used both as a CO 2 sorbent and as a feedstock for the production of clinker.21–23 Moreover, the integration of calcium looping in existing cement plants is simpler than other promising alternatives, such as the oxy-fuel combustionReaction Chemistry & Engineering RSC Publishing
احصل على السعر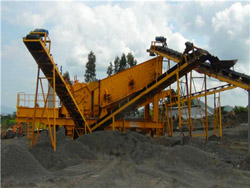
Cement Manufacturing Process INFINITY FOR CEMENT EQUIPMENT
Cement raw meal activation for discharge is achieved by slight aeration. For that purpose compressed air is introduced through a permeable media covering the silo bottom. To save energy modern cement plants preheat the raw material before they enter the kiln. Rising more than hundred meter, hot exit gases from the kiln heat the raw meal asThe HCl absorption by cement raw meals was experimentally evaluated in the temperature range 100-180℃, using a fixed-bed set-up and gas phase HCl content between 50ppmv and 200ppmv. HCl is a gaseous pollutant of concern in the cement industry with serious environmental impact. A significant number of cement plants are Experimental evaluation of hydrogen chloride (HCl) absorption by cement
احصل على السعر
Natural Resources Exploitation in Sulfate-Resisting
The raw materials (ordinary limestone, black marl, grey marl, and iron ore) used for the ordinary Portland cement production in the SCB cement plant were not sufficient to produce SR raw meals. Thus, The calcium looping CO 2 capture process, CaL, represents a promising option for the decarbonisation of cement plants, due to the intrinsic benefit of using the spent CO 2 sorbent as a feedstock for the plant. The Calcination kinetics of cement raw meals under
احصل على السعر
Energetic assessment of a precalcining rotary kiln in a cement plant
The solid (kiln feed-raw meal) mixed with the gas flow below in each mixer; assumed heat exchange in the process. The mixture was sent to a cyclone and separated. The temperatures of the gas and solids assumed the same in each cyclone stage. The efficiency of each cyclone is set to reflect the dust emission of the reference cement plant Tokyo. Japan 1986 OPTIMIZATION OF CEMENT MANUFACTURING PROCESS G. Nakamura, T. Aizawa and K. Nakase Onoda Cement Co., Ltd., 1-1-7, Toyosu Koto-ku, Tokyo,japan Abstract. Cement manufacturing process is now operated with the aid of various control systems, such as raw meal compositi on control, kiln control and mill Optimization of Cement Manufacturing Process ScienceDirect
احصل على السعر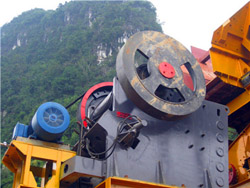
Reactivity of calcined cement raw meals for carbonation
The use of raw meals as a CO 2 sorbent is a relatively recent concept, but it is an interesting alternative to evaluate with the aim of achieving zero emissions for cement manufacturing plants [14,19,20,22,23,30,31]. Raw meal is a mixture of fine powdered limestone, silica, alumina and iron oxide and only the CaO present in the limestone isThis process is critical for clinker production as raw meal calcination affects the clinker quality, plant operation, and environmental emissions . A calciner is a preferred option for AF firing since it requires a low temperature (800–900 °C) for calcination compared to clinkerisation (1400–1450 °C) in the kiln.Recent Progress in Refuse Derived Fuel (RDF) Co-processing in Cement
احصل على السعر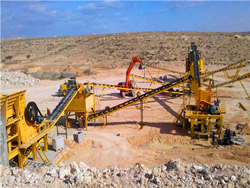
Cement substitution with secondary materials can reduce
The system boundaries included raw materials extraction and transport to the cement plant, pretreatment and pyroprocessing of raw meal for clinker, transport of secondary CMs to the cement plantLime Component Limestone: Common forms of calcium carbonate used as raw material for cement manufacturing are limestone and chalk.Limestone is of predominantly fine grained crystalline structure, its hardness is between 1.8 to 3.0 of the Mohs scale of hardness and specific gravity 2. To 2.8. Limestone usually contains admixtures of clay substance or Raw materials for cement manufacturing Cement Plant
احصل على السعر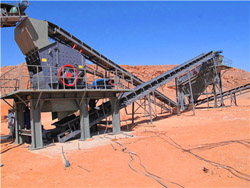
About Cement Cement
The process begins with the mined raw materials being ground into a raw meal ready for the kiln. This precise mixture of ground limestone, clay and sand is heated in the precalciner before being fed into the kiln where it is transformed (calcined) into clinker at very high temperatures typically around 1,450˚C.Vertical roller mills (VRMs) with integrated classifiers have been used successfully for many years in cement plants to grind and dry raw materials simultaneously with moisture contents up to 20% by weight. G. Grasa, and R. Murillo, “Reactivity of calcined cement raw meals for carbonation,” Powder Technology, vol. 354, pp. 338–347A Review on Pyroprocessing Techniques for Selected Wastes
احصل على السعر