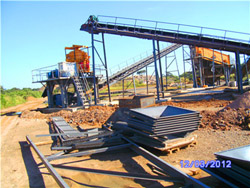
(PDF) Iron Ore Pelletizing Process: An Overview
PDF On Jul 11, 2018, Sandra Lúcia de Moraes and others published Iron Ore Pelletizing Process: An Overview Find, read and cite all the The iron ore pelletizing process consists of three main steps: 1. Pelletizing feed preparation and mixing: the raw material (iron ore concentrate, additives anthracite, Iron Ore Pelletizing Process: An Overview IntechOpen
احصل على السعر
Iron Ore Pelletization: Part I. Fundamentals
A framework which describes how these binders interact not just with the pellet feed but also with each other is developed. This part describes the history, goals of Modern iron ore pelletizing process operations may be divided into two main process sections: feedstock preparation and agglomeration processes. In most Development of a Novel Grinding Process to Iron Ore Pelletizing
احصل على السعر
Iron ore pelletization ScienceDirect
Abstract. A brief introduction to recent developments in iron ore pelletizing is provided in this chapter, including the world output of fired pellets, pellet production rotary kiln; kiln aerodynamics; turbulence; mixing; combustion; CFD; experiments. 1. Introduction. The pelletizing process, where the crude ore from the mine The Aerodynamics of an Iron Ore Pelletizing Rotary Kiln
احصل على السعر
-The 3 basic stages of any Pelletizing Process
Nov 2020 Sławomir Obidziński Magdalena Joka Yildiz The paper presents the results of the pelletization (agglomeration) tests of post-harvest tobacco waste as a feedstock for fuel pellet production....Iron ore pellets are an essential part of the blast furnace charge, with high grade, good strength, uniform particle size, good metallurgical properties, and so forth. 1, Iron Ore Pelletization: Part I. Fundamentals Request PDF
احصل على السعر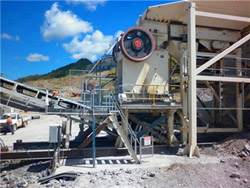
Iron Ore Pelletizing Process: An preview & related info
(2018) Moraes et al. Iron Ores and Iron Oxide Materials. The iron ore production has significantly expanded in recent years, owing to increasing steel demands in developing Iron ore concentration typically involves comminution, separation, and agglomeration. and provides a framework so that the chemical factors leading into an effective pelletizing process can be understood. The general overview of binders is covered to provide an outline of what binding mechanisms are present, but details regarding Iron Ore Pelletization: Part I. Fundamentals
احصل على السعر
Degradation mechanism of high alumina refractory bricks by
The most widely used industrial process for pellet induration is the grate-kiln process in China [[7], [8], [9]]. The iron ore is first crushed into a powder, mixed with additives and a binder, and rolled into green pellets (10–15 mm in diameter) that are sintered to pellets in a furnace during pelletizing of iron ore [10,11].The traveling grate indurating process is responsible for two-thirds of the world’s installed pelletizing capacity. TON Outotec offers the industry’s leading induration technology for iron ore pellet processing, which is based on over 60 years of experience and world-class R&D. This process produces pellets with excellent physicalNextGen Pelletizing™ TON
احصل على السعر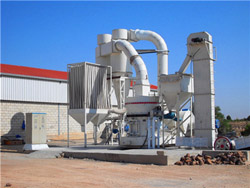
Investigation on low energy-consumed embedded selective
In the long-process of iron-making, the pelletizing process is a key step to turn iron ore into pellet (Guo et al. 2017, Purohit et al. 2018). Compared with sinter, pellet exhibits the advantage of lower pollutant and carbon emission. The emission intensities of SO 2, NO x, and CO 2 for pellet are 1/3 ~ 1/2 of those for sinter. Increasing theIron ore pelletizing is a two-step process. This begins with the formation of green pellets with the addition of a binder to improve agglomeration phenomena. Then it follows an induration process to obtain appropriate mechanical and Mechanism of magnetite iron ore concentrate morphology
احصل على السعر
Pelletizing SpringerLink
Pelletizing, in ironmaking, is a process used to agglomerate iron ore concentrates with a granulometry <150 µm and low concentration of impurities.Iron ore concentrates are mixed with water, bentonite, and hydrated lime (cold agglomeration) and are treated in a rotary disk to form round agglomerates (green pellets) with sizes After the pelletizing process, the iron ore powder forms green pellets of uniform size. To facilitate transportation and processing, green and dry pellets must be of a certain strength. The important indicator used to evaluate the strength of green pellets is the green pellet drop number, which is generally required to be from 4–6 timesPolymers Free Full-Text A Review on the Effect of the
احصل على السعر
Effects of Pellet Basicity on the Simulated Deposit Formation
The pelletizing process’s energy consumption, CO 2 emission, and environmental pollution are much lower than the sintering process. In order to optimize the structure of the blast furnace burden and reduce the environmental pollution, (6) some companies have focused on the production of fluxed iron ore pellets to replace the iron ore sinterThe iron ore pelletizing process consists of three main steps: 1. Pelletizing feed preparation and mixing: the raw material (iron ore concentrate, additives anthracite, dolomite and binders are prepared in terms of particle size and chemical specifications, dosed, and mixed together to feed the pelletizing process; 2.Iron Ore Pelletizing Process: An Overview IntechOpen
احصل على السعر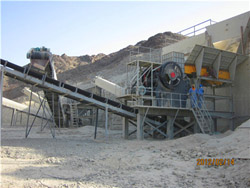
Iron Ore Pelletization FEECO International Inc.
In addition to mined iron ore, other sources of iron, such as flue dust collected from blast furnaces, or the dust produced at mine sites, can be recovered and incorporated into the pelletizing process to avoid wasting any iron-bearing material. The Pelletizing Process. The production of iron ore pellets from fines to finished product canThe pelletizing process, where the crude ore from the mine is upgraded, involves several steps, including grinding, balling, and induration; see Figure 1 to the left. In the grate-kiln induration process []—see Figure 1 to the right—the sintering is mainly taking place in a rotary kiln, where the pellets increase their strength and metallurgical properties.The Aerodynamics of an Iron Ore Pelletizing Rotary Kiln
احصل على السعر
Life cycle energy consumption and greenhouse gas emissions of iron
Compared with iron sintering, pelletizing process is more environmentally friendly with lower energy consumption and less GHG emissions. In addition, the SO 2, NOx and dust emissions of pelletizing are ≤5% of sintering process. Efforts to further improve the pelletizing technologies are addressed to catch up the global technological frontierThis part describes the history, goals of pelletization, and provides a framework so that the chemical factors leading into an effective pelletizing process can be understood. The general overview of binders is covered to provide an outline of what binding mechanisms are present, but details regarding specific binders will be explicated furtherIron Ore Pelletization: Part I. Fundamentals Semantic Scholar
احصل على السعر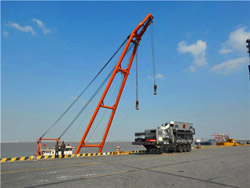
Iron Ores and Iron Oxide Materials IntechOpen
Iron remains the basis of modern civilization, and our sustainable future deeply depends upon our ability to satisfy the growing demand for iron and steel while decoupling hazardous emissions from economic growth. Therefore, environmental sustainability aspects are also broadly addressed. Iron Ore Pelletizing Process: An The pelletizing process has lower energy consumption and less pollution emission compared with iron ore sintering process. Its superiority made it a significant way for the cleaner production of iron making. Usually, the high-grade iron ore is Improvement on the thermal cracking performance of
احصل على السعر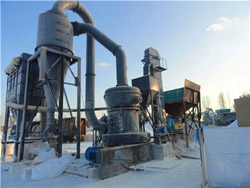
Research on the ring formation mechanism of magnesian
The effect of co-firing coal and woody biomass upon the slagging/deposition tendency in iron-ore pelletizing grate-kiln plants. Fuel Process. Technol. 199,106254–106270 (2020).1.1.3.2.2.1 Pelletizing Process. Similar to sintering, pelletizing is another widely used process to agglomerate the iron ore. Sinter plants are usually located near the blast furnace plant, but pelletizing plants are often located near the mining site. Some works have both pelletizing and sintering plants at the smelter sites. 1.1.3.2.2.2Pelletization an overview ScienceDirect Topics
احصل على السعر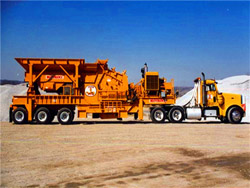
KOBELCO Pelletizing Process
KOBELCO TECHNOLOGY REVIEW NO. 29 DEC. 2010 58 KOBELCO Pelletizing Process Shinichi YAMAGUCHI*1, Takeshi FUJII *1, Norihito YAMAMOTO,Tsutomu NOMURA*2 *1 Plant Engineering Department, Iron Unit Division, Natural Resources & Engineering Business, *2 Technology & Process Engineering Department, Portfolio of online digital tools covering the important steps of the pelletizing process. For the particle size measurement TON Outotec has its technologies like the online sampling and analysis system PSI 500 R, which measures the particle size distribution (PSD) of ground concentrate, with a target of maintaining the concentrate Next generation of pelletizing plants for the transition to
احصل على السعر
Effect of Blaine Number on the Physical and Mechanical
The iron ore concentrates and different binders (bentonite, lime, limestone, and Cement) are mixed in calculated proportions and placed in a disk pelletizer with a 1 m diameter for pelletizing. The ratio of iron ore concentrates and binder mixture for different pellets is shown in Table 3. The disk angle and speed of the pelletizer are fixed as
احصل على السعر